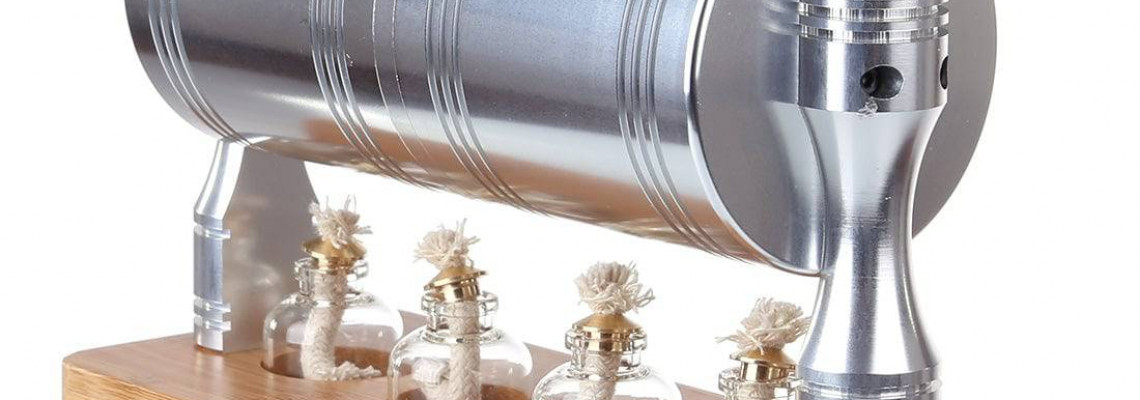
1.2 kW, the Green Turbine
We create and produce the 1.2 kW green turbine. Green turbines are low-CO2, environmentally beneficial ways to generate electricity. They are of good quality and reasonably priced.
1.2 kW, the Green Turbine
Steam powers a turbine in the Green Turbine, a small-scale power generation device that produces electricity. It is intended for small-scale off-grid applications and has a rated output of 1.2 kW. The Green Turbine is made up of multiple parts:
Boiler: The boiler produces steam by heating water. The Green Turbine is designed to operate with gas-fired and wood-fired boilers.
Steam turbine: The steam turbine is at the core of the Green Turbine system. This compact, fast turbine is highly efficient. To power a generator, the steam turbine transforms the energy contained in the
steam into rotational energy.
Generator: The generator is in charge of turning the steam turbine's rotational energy into electrical energy. A range of generators, including both AC and DC generators, can be used with the Green Turbine.
Control system: The control system monitors and manages the Green Turbine's operation. It has a controller to change the turbine's speed and sensors to monitor the steam's temperature and pressure.
Condenser: Following its passage through the turbine, the steam is cooled in the condenser. This allows the steam to condense back into water, which may then be heated once more in the boiler.
Exhaust system: The combustion process's exhaust gases are extracted via the exhaust system. This enhances the system's efficiency and lowers emissions.
The Green Turbine is a tiny, effective power generation device that works well for off-grid small-scale applications. It can offer a dependable electricity supply in isolated or rural locations without grid power and is simple to install and maintain.
Boiler
A boiler is a specialized system or vessel producing steam or heat water. It is essential to many sectors and uses, such as industrial processes, heating systems, and power generation. Here are some indispensable boiler facts:
Function: A boiler's primary job is to use heat energy to turn water into steam. The boiler's steam can be used to generate electricity, heat buildings, supply hot water, or power industrial operations, among other uses.
Parts: A boiler usually has a fuel supply (coal, oil, natural gas, biomass, etc.), a burner or heating element, a combustion chamber, a heat exchanger, a water or steam circulation system, and control systems for controlling pressure and temperature.
Boiler Types: Water-tube and fire-tube boilers are two of the various types of boilers. Steam is produced in a fire-tube boiler when hot gases from combustion pass through tubes submerged in water, heating the water. In a water-tube boiler, steam is produced as hot gases flow around the tubes and water circulates inside.
Efficiency: The capacity of a boiler to transform fuel into sound thermal energy is known as boiler efficiency, and increased boiler efficiency results in less energy waste and more effective fuel use. A number of strategies, including heat recovery systems, insulation, and combustion optimization, can increase efficiency.
Safety: Safety is crucial because boilers work at high temperatures and pressures. To guarantee safe and dependable operation, safety elements like flame safeguard systems, water level controls, and pressure relief valves are implemented.
Maintenance: Routine maintenance is necessary for boilers to operate safely and effectively. This covers regular examinations, heat exchanger cleaning, burner upkeep, and water treatment to prevent corrosion and scaling.
Environmental Considerations: Boilers can mainly affect the environment by emitting pollutants, including sulfur dioxide (SO2), nitrogen oxides (NOx), and carbon dioxide (CO2). However, efforts are being made to increase boiler efficiency and lower emissions by using cleaner fuels or renewable energy sources, flue gas treatment systems, and sophisticated combustion technologies.
When choosing a boiler, the necessary steam or heat capacity, fuel availability, cost, efficiency, emissions, and regulatory compliance are all critical considerations. Speaking with boiler manufacturers or specialists can help you select the right boiler for a given application.
A steam turbine is an apparatus that transforms pressurized steam's thermal energy into mechanical work that can be utilized to produce electricity or carry out other mechanical operations. It is an essential feature of many power plants, especially those that use steam as their primary source of electricity. The following are some crucial details regarding steam turbines:
Principle of Operation: The laws of conservation of energy and thermodynamics underpin the functioning of steam turbines. After entering the turbine, pressurized steam passes through a number of spinning and stationary blades. The steam expands and applies force to the blades as it passes through them because of its temperature and pressure drop. The rotor rotates as a result of this force, and the spinning blades' kinetic energy is transformed into mechanical work.
Types of Steam Turbines: Impulse and reaction turbines are two types of steam turbines. Reaction turbines are employed in higher-pressure and higher-power applications, whereas impulse turbines are usually used in low-pressure applications. The design and arrangement of the blades and stages determine the variations within each type.
Components: A steam turbine consists of a rotor, stationary blades or nozzles, diaphragms, and casing. The turbine's revolving component, the rotor, is attached to a mechanical device or generator. The diaphragms divide the various pressure levels, and the stationary blades or nozzles guide the steam flow onto the rotor blades. The casing supports and houses the turbine's parts.
Power Generation: In thermal power plants, such as coal-fired, natural gas-fired, and nuclear power plants, steam turbines are frequently utilized to generate electricity. The boiler's steam is sent into the turbine, which expands and powers the rotor, producing energy. A generator, which transforms the mechanical energy into electrical energy, is connected to the turbine's spin.
Efficiency and Performance: Steam turbine efficiency is a key component of power plant performance. Turbine design, steam parameters (temperature and pressure), steam quality, and control systems are some of the elements that affect efficiency. Higher turbine efficiencies result in better conversion of thermal energy into mechanical work, which raises the efficiency of the power plant as a whole.
Operation and Maintenance: Steam turbines need to be regularly maintained and observed to guarantee optimum performance. This covers routine maintenance, cleaning, lubrication, and inspections. To ensure safe and effective operation, sophisticated control systems regulate the steam flow, temperature, and pressure.
Applications outside of power generation: Steam turbines are employed in a number of industrial processes, including the powering of compressors, pumps, and other machinery. They can be found in sectors where steam is frequently used, like oil and gas, chemical processing, and refining.
Since their widespread use over the years, steam turbines have remained an essential technology for industrial and power generation applications. Continuous improvements in turbine design, materials, and control systems aim to improve efficiency, dependability, and environmental performance.
Generator
An apparatus that transforms mechanical energy into electrical energy is called a generator. It is made up of a number of parts that combine to generate power. Key information regarding generators is as follows:
Principle of Operation: Electromagnetic induction is the basis for generator operation. An electric current is created in a conductor when it is moved through a magnetic field or when a magnetic field is moved through a stationary conductor. This is typically the case with a coil of wire. Electrical energy is produced from mechanical energy in generators by means of this phenomenon.
Components: A generator's primary parts consist of:
The generator's revolving component that houses a collection of magnets or a coil of wire is called the rotor or armature.
The generator's stationary stator encircles the rotor and is filled with wire coils.
Exciter: A little generator or electromagnet that gives the rotor its first magnetic field.
Prime Mover: The prime mover is the mechanical apparatus that supplies the mechanical energy needed to run the generator, such as a wind turbine, gas engine, or steam turbine.
Voltage Regulator: A control mechanism that manages the generator's output voltage.
Types of Generators: Generators can be divided into a number of types according to their construction and power source. Typical varieties include:
Alternating Current (AC) Generators: AC generators generate electrical power in the form of alternating current. They are extensively utilized in most electrical applications and power generation.
Direct Current (DC) Generators: DC generators generate electricity in direct current. Battery charging systems and other industrial applications frequently employ them.
Portable Generators: These are compact, standalone generators made for short-term or transportable power requirements, like emergency backup power, construction sites, or camping.
Standby Generators: During utility power outages, standby generators are intended to supply backup power automatically. They are frequently utilized in commercial, industrial, and residential contexts.
Power Rating: A generator's power output, commonly expressed in megawatts (MW) or kilowatts (kW), determines its rating. The power rating is an essential factor to consider when choosing a generator for a particular application, as it establishes the electrical load that the generator can manage.
Applications: There are many different uses for generators, such as:
Backup Power: In order to supply electricity during utility power outages, generators are frequently utilized as backup power sources in commercial, industrial, and residential contexts.
Rural Areas and Off-Grid Power: Generators are frequently utilized in places without access to a centralized power grid, such as rural areas or off-grid locales.
Construction and Industrial Sites: When a dependable power source is required, generators are utilized to supply temporary electricity on building sites or in industrial environments.
Emergency Services: Generators are essential for supplying power to emergency services like hospitals, fire stations, and emergency response centers during emergencies to ensure continued operation.
Generators are crucial for supplying electricity in various scenarios, such as powering isolated areas or serving as a backup during blackouts. Different criteria, including budget, application, fuel type, and power requirements, influence a generator's choice. Regular maintenance and correct operation are essential for the generator to operate at its best and last a long time.
Why 1.2 kW, the Green Turbine?
The Green Turbine is a low-carbon, sustainable, and eco-friendly technology that tries to lower greenhouse gas emissions and encourage the creation of renewable energy, hence its name. Small-scale steam turbines, which are driven by steam generated from any heat source, including biomass, solar, geothermal, waste heat, and other renewable or waste fuels, are intended to produce electricity. The Green Turbine can offer a cost-effective and efficient solution for decentralized power generation, off-grid and remote locations, and sustainable energy projects by utilizing a range of heat sources.
A steam turbine is a machine that transforms steam's thermal energy into mechanical energy, which can be utilized to produce mechanical work or electricity. Power plants, businesses, and maritime applications all make extensive use of steam turbines.
The essential operation of a steam turbine is as follows:
Steam Production: Heating water produces steam. Burning fossil fuels (coal, natural gas, and oil), employing nuclear processes, or utilizing renewable energy sources like solar or geothermal can all help achieve this.
Steam Expansion: The steam turbine receives the high-pressure steam generated in the boiler. When it enters the turbine, the steam experiences high pressure and velocity.
Blades and Rotors: Rotors have blades that allow steam to pass through them. The rotor rotates as the steam flows across these blades. A shaft is attached to the rotating rotor.
Mechanical Work: The revolving rotor's kinetic energy is transformed into mechanical work. This work can be utilized to operate machines, turn an electrical generator, and carry out other duties.
Exhaust: The steam leaves the turbine at a reduced temperature and pressure after going past the turbine blades. After condensing back into water, this low-pressure steam is put back into the boiler to be heated and used once more.
Steam Generation for a Steam Turbine
The process of creating steam from water is known as steam generation. Among the many uses for this steam are industrial operations, heating, and power generation. The boiler, which heats water to create steam, is the most often used technique of producing steam. An outline of the steam-generating process is provided below:
Boiler: A boiler is an apparatus that uses thermal energy to turn water into steam. Fuels like coal, natural gas, oil, or biomass are typically burned to produce heat, or electricity or renewable energy sources like solar or geothermal are used.
Combustion or Heat Source: In boilers that burn fossil fuels, heat is released during combustion, which takes place in a combustion chamber. The boiler's water temperature is raised by transferring the heat produced.
Water Feed: A feedwater system supplies water to the boiler. This can be an ongoing procedure to keep the boiler's water supply consistent.
Heat Transfer: The water in the boiler receives heat from the combustion process. As a result, the water reaches a temperature where steam is produced.
Steam Formation: Water changes from a liquid to a vapor as it absorbs heat. The boiler's upper section then collects the generated steam.
Superheating (optional): To raise the steam's temperature and energy content, it may occasionally be heated further. Superheating is the term for this process, which takes place in a different area of the boiler.
Steam Distribution: The produced steam can be dispersed via pipelines for a variety of uses. Steam is frequently utilized in power plants to rotate turbines connected to generators to generate electricity. Steam is also used in industrial processes for drying, heating, and other production tasks.
Boiler
A closed vessel or device used to heat water or other liquids is called a boiler. Because it is crucial to the production of steam for power generation, heating systems, and industrial processes, it is a necessary part of many different industries. A boiler's primary job is to deliver heat energy to water in order to turn it into steam. The main parts and varieties of boilers are as follows:
Essential Elements of a Boiler:
Burner: The burner is in charge of burning fuel to provide heat energy. Coal, oil, biomass, and natural gas are examples of standard fuels. Heat is released into the combustion chamber by the hob.
Combustion Chamber: The furnace or combustion chamber is where heat is produced by burning fuel. Its purpose is to regulate and confine the combustion process.
Heat Exchanger: The heat exchanger turns water into steam by transferring heat from combustion gases to the water. There are several types of heat exchangers, such as coil-type, water-tube, and fire-tube designs.
Water or Steam Drum: The water or steam is stored in the drum. Several drums can be employed in water-tube boilers to divide the various phases of the steam production process.
Tubes or Coils: Heat is transferred to the water via tubes or coils, which are the channels via which hot gases or combustion products pass. Whereas the water in water-tube boilers passes through the tubes, the water in fire-tube boilers is contained within the tubes.
Boiler Shell: The pressure vessel and other parts are housed in the boiler shell, which is the outside cylindrical section. It offers protection and structural support.
Controls and Instrumentation: To monitor and control the combustion process, water level, pressure, and other parameters, boilers are outfitted with a variety of controls and instruments.
Boiler Types:
Boilers with fire tubes: These boilers use hot gases that travel via water-enclosed tubes. Steam is created when heat is passed from the tubes to the water. Fire-tube boilers are usually used for applications requiring low to medium pressure.
Water-Tube Boilers: In water-tube boilers, combustion gases circulate tubes that carry water. Prominent industrial locations and high-pressure applications are common uses for water-tube boilers.
Electric Boilers: These boilers produce heat using electricity and are appropriate for uses where alternative fuel sources might not be feasible.
Biomass Boilers: These boilers run on organic fuels like wood or agricultural waste.
Circulating Fluidised Bed (CFB) Boilers: CFB boilers effectively burn solid fuels using a fluidized bed of particles.
The application, the necessary steam pressure, and the availability of fuel all influence the type of boiler chosen. Boilers play a vital role in producing heat and steam for a variety of commercial and industrial processes, which significantly aids in the generation of energy and other manufacturing activities.
Combustion or Heat Source
Boiler with three passes (6 bar; higher pressure ratings upon request)
Heat exchanger for safety (built inside boiler)
Chamber of combustion
Ports that blow in
Secondary air injection
Flue gas recirculation injection
A water-cooled screw is used to remove ash from the combustion chamber automatically.
The door of the firebox
Optional pneumatic boiler tube dedusting
One essential part of a boiler that produces the thermal energy required to turn water into steam is the combustion or heat source. A fuel is burned during the combustion process to release heat, and the fuel selection is influenced by several factors, including cost, availability, and environmental concerns. Boilers frequently use the following fuels:
Natural gas: A popular fossil fuel for power generation and heating that burns cleanly. In comparison to other fossil fuels, it emits fewer emissions.
Oil (Diesel or Heavy Fuel Oil): Liquid fuels frequently used in boilers, particularly in places with limited access to natural gas.
Coal: A common and conventional fuel for boilers, particularly in power plants. However, more carbon dioxide and other pollutants are released when coal is burned than when gas is used.
Biomass: Boilers can be powered by biomass, which includes organic resources like wood, crop wastes, and animal manure. As a renewable resource, biomass can help lower greenhouse gas emissions.
Electricity: Some boilers run on electricity as their heat source. This technique is frequently employed in places where alternative fuel sources are costly or impracticable.
Renewable Energy Sources: Boilers can occasionally produce heat using renewable energy sources, such as geothermal or solar power.
Usually, the boiler's furnace or combustion chamber is where the combustion process occurs. The following are the main steps in combustion:
Fuel Combustion: After entering the combustion chamber, the fuel combines with ambient oxygen to undergo combustion. Heat energy is released during this chemical process.
Flame Formation: The heat produced by the combustion reaction creates a flame, which heats the boiler's surfaces, such as the radiator or tubes.
Transfer of Heat: The heat from the combustion process is transmitted to the water or other fluid in the boiler. As a result of this heat transfer, steam is created when the water reaches its boiling point.
Control of Combustion: Boiler combustion is meticulously regulated to guarantee safe and effective operation. To maximize combustion efficiency and reduce emissions, variables such as temperature, pressure, and the ratio of fuel to air must be monitored.
A boiler system's overall performance depends on efficient combustion. To ensure maximum efficiency, low environmental impact, and safe operation, modern boilers frequently integrate sophisticated control systems to regulate the combustion process.
Water Feed
One of the most essential parts of a boiler that controls the water supply for steam production is the water feed system. This system keeps the water level at the required level by ensuring a steady and regulated water supply to the boiler. The water feed must be correct for a boiler to operate safely and effectively. The water feed system normally operates as follows:
Water Source: The water feed system begins with a water source, which, depending on the use, may originate from a well, the city water supply, or another source.
Makeup Water: As steam is produced in many boiler systems, some water is constantly lost and must be replenished. Makeup water is a common term for this replacement water.
Feedwater Pump: The feedwater pump is a component of the water feed system that supplies the boiler with makeup water. The pump guarantees a steady flow of water into the boiler.
Feedwater Control Valve: A control valve is frequently placed to manage the water flow into the boiler. Usually, a level sensor or controller that keeps track of the boiler's water level controls this valve. The valve opens or closes to maintain the appropriate water level and modify the water flow.
Preheating (Optional): In specific boiler systems, makeup water may be preheated before entering the boiler. Preheating the water using waste heat from flue gases or other sources can increase energy efficiency.
Water Treatment: Depending on the quality of the water source, water treatment procedures may be used to eliminate contaminants and stop scale or corrosion inside the boiler. This is critical to the boiler's longevity and effective functioning.
Optional Expansion Tank: Closed-loop systems may employ an expansion tank to account for temperature-related changes in water volume. This tank helps keep the system's pressure steady.
The water supply system intends to maintain the boiler's water level. If the water level is too low, the boiler tubes or heating surfaces may be subjected to high heat, which could cause damage. However, if the water level is too high, water may flow over into the steam, which could lead to problems with operation and lower system efficiency.
Proper water feed control, frequently automated using control systems to guarantee accurate and constant water flow management, is essential for the safe and effective operation of boilers. Routine water feed system maintenance and observation are also important parts of boiler management.
Heat Transfer
Heat transfer is the process by which thermal energy is transferred between various parts of a system or between systems. Heat is transferred primarily by conduction, convection, and radiation.
Conduction
Conduction is the process by which heat is transferred through a substance without the substance moving. It happens when nearby molecules or atoms exchange kinetic energy with one another.
For instance, when a metal rod is heated at one end, the heat energy is transferred through the material and warms the other end.
Convection
Convection is the process by which the motion of fluids, such as liquids or gases, transfers heat. It occurs as a result of fluid circulation caused by temperature variations.
As an illustration, when water is heated in a pot on a stove, hot water rises and forms a circulation pattern. A constant flow of heat is produced when cooler water descends to replenish the hot water as it grows.
Radiation
The transfer of heat via electromagnetic waves, including infrared radiation, is known as radiation. Radiation can happen in a vacuum and doesn't need a medium like conduction and convection do.
For instance, the Earth receives heat from the Sun through radiation. Heat is also radiated via a heated electric coil in an electric cooker.
The effectiveness of each heat transfer method depends on the specific conditions and materials involved. In many real-world situations, multiple methods may co-occur.
Uses
Cooking: Heat transfer is essential when cooking. For instance, convection occurs when water boils, radiation occurs when food is grilled or roasted, and conduction happens when a pan is heated on a stove.
Engineering: The design of effective heat exchangers, electronic cooling systems, and insulation materials are just a few of the many engineering applications where heat transmission is essential.
Climate Control: HVAC systems heat or cool buildings using heat transfer principles. Air conditioning systems, for example, remove heat from indoor environments by using a combination of conduction, convection, and occasionally radiation.
Power Generation: Heat transfer plays a crucial role in power plants' transformation of thermal energy into mechanical and electrical energy. For instance, steam turbines use heat transfer to produce electricity.
Designing effective systems, increasing energy efficiency, and avoiding undesirable consequences like overheating or heat loss all depend on an understanding of and ability to control heat transfer processes.
Steam Formation
A phase-change process known as "steam formation" transforms water from a liquid to a gas, which is what we usually call "steam." When water absorbs enough thermal energy to overcome the latent heat of vaporization, this process takes place. This is a broad summary of how steam forms:
Heat Application:
Heat is applied to water to create steam. Burning fossil fuels, nuclear processes, or renewable energy sources like solar or geothermal can all produce heat.
Rise in Temperature:
Water's temperature increases as heat is applied. At standard atmospheric pressure, water boils at 100 degrees Celsius (212 degrees Fahrenheit). Pressure raises the boiling point.
Heating up:
Additional heat application does not raise the water temperature when it reaches its boiling point at a specific pressure. Instead, the heat absorbed turns the water into steam.
Phase Shift:
The latent heat of vaporization is absorbed during the phase transition from liquid to gas. Without changing the temperature, this energy is needed to break the bonds holding water molecules together and turn them from a liquid to a gas.
Steam is the resultant Vapor, which is made up of water molecules. Because of its high energy content and workability, steam is a valuable resource for various purposes.
Optional Expansion:
In some systems, steam can be further expanded or superheated, raising its temperature above the boiling point. This may improve its energy content and particular qualities.
One essential component of steam turbine power generation is the steam creation process. In power plants, steam is poured onto turbine blades after water is cooked in a boiler. Steam expands inside the turbine, producing mechanical energy that turns generators to create electricity.
Superheating
The method of superheating involves heating steam over its saturation point, or the temperature at which it would typically boil at a specific pressure. In other words, superheated steam is steam that has been heated even further after it has reached the boiling point and vaporized fully.
The following are the main attributes of superheated steam:
Increase in Temperature: The temperature of superheated steam is higher than the saturation temperature corresponding to its pressure. Superheated steam's temperature is frequently expressed in degrees Celsius or Fahrenheit.
No Saturation: Superheated steam is entirely Vapor, as opposed to saturated steam, which is at the boiling point for a given pressure and comprises both liquid and vapor phases.
Greater Energy Content: At the same pressure and volume, superheated steam has a higher energy content per unit mass than saturated steam. This increases its work capacity and benefits specific industrial processes.
Superheating steam is usually accomplished in a separate boiler section or a special superheater. This is how it usually operates:
Boiling Water: In a boiler, boiling water creates saturated steam as the first stage.
Separation: To guarantee that the saturated steam is in a pure vapor form, it is then separated from any leftover water droplets.
Section for Superheating: Next, the steam passes through a heat exchanger called a superheater, which is intended to give the steam more heat. This raises the steam's temperature without affecting its pressure.
Controlled Temperature: To reach the required level of superheat, the steam's temperature exiting the superheater can be adjusted.
There are multiple reasons why superheated steam is used in power generation and other industrial processes:
Enhanced Efficiency: In power plants, where it is used to drive turbines more efficiently, superheated steam can improve the efficiency of specific processes.
Preventing Condensation: Superheating helps prevent steam from losing energy by keeping steam pipes dry and controlling the production of water droplets.
Better Heat Transfer: Superheated steam may be helpful when a high-temperature heat source is needed for specific heat transfer applications.
It's vital to remember that superheater design and application are contingent upon the particular needs of the industrial or power-generating process, and factors like system efficiency and safety are critical to their execution.
Steam Distribution
In order to use steam for a variety of commercial, industrial, and domestic purposes, it must be transported and delivered from the site of generation—such as a boiler—to the points of use. For processes that depend on steam to operate successfully, steam distribution systems must be both safe and efficient. Key elements of steam distribution are as follows:
System of Piping:
A system of pipes carries steam from the boiler to several locations for use. The piping system needs to be insulated to reduce heat loss and built to withstand the high temperatures and pressures involved with steam.
Controls and Valves:
Valves manage the steam flow in the distribution system. Control valves and other devices adjust the steam's temperature, pressure, and flow rate at various locations to satisfy the unique needs of the machinery or processes being supplied.
Steam traps:
Steam traps are devices inserted in the steam distribution system to remove condensate or liquid water that occurs when steam cools during transit. Proper condensate evacuation is crucial for maintaining the system's effectiveness and avoiding equipment damage.
Stations that Reduce Pressure:
Pressure-reducing stations, which usually have valves that lower the pressure of high-pressure steam to a level appropriate for specific uses, are frequently used in steam distribution networks.
Safety Equipment:
Pressure relief valves and other safety measures are fitted to guard against overpressure in the equipment and steam distribution system. These tools aid in preventing system damage and ensuring worker safety.
Meters for steam:
Steam meters measure the quantity of steam used at various locations across the distribution system. This data is crucial for monitoring energy use, improving system performance, and controlling expenses.
System for Condensate Return:
A condensate return system returns condensate, created when steam loses heat energy, to the boiler. As a result, less water makeup is required, and the water can be reused.
Insulation:
Steam pipes must be well insulated to reduce heat loss and keep steam at a consistent temperature while being transported. Fibreglass, foam, and other materials appropriate for high-temperature applications are examples of insulation materials.
Distribution of Steam in Power Plants:
Steam is transferred from the boiler to the turbines in power plants to produce mechanical power. The high-pressure steam then condenses back into water and is returned to the boiler.
Efficient steam distribution is essential for optimizing energy efficiency, cutting operating costs, and guaranteeing the dependability of steam-dependent processes. Regular maintenance, observation, and adherence to safety regulations are also necessary for steam distribution systems to operate safely and effectively.
Expansion of Steam
The process by which steam expands as it passes from a higher pressure to a lower pressure is known as steam expansion. This expansion is a vital component of many steam-based systems, especially those used in power generation.
In the context of a steam turbine in a power plant, the expansion of steam usually happens as follows:
Steam at High Pressure:
A boiler produces steam at high temperatures and pressures. The steam turbine's blades are the target of this high-pressure steam.
Blades of a turbine:
The high-pressure steam transfers its high kinetic energy to the turbine's blades as it passes over them, spinning them.
Mechanical Tasks:
A shaft is attached to the rotating turbine blades, which exert mechanical force on the shaft as they rotate. A generator receives this mechanical labor and transforms it into electrical energy.
Growth:
Steam expands significantly as it moves past the turbine blades. Its temperature and pressure drop while its volume rises, resulting from the energy of the steam being transformed into mechanical work.
Steam at Low Pressure:
The pressure and temperature of the steam leaving the turbine have decreased. To extract more work from the steam, this low-pressure steam may occasionally be routed to further turbine stages.
Optional Condensation:
During some power generation cycles, the low-pressure steam may condense back into water, which is then put back into the boiler to start the process over.
The expansion of steam in a turbine is a crucial stage in transforming thermal energy into mechanical energy, which is then converted into electrical energy. The design of the turbine, the steam's temperature and pressure, and the power plant's general layout all affect the efficiency of this process.
It's important to remember that steam expansion can also happen in industrial operations when steam is utilized for heating or mechanical activity in addition to electricity generation. Optimizing the performance and efficiency of steam-based systems requires an understanding of and control over the expansion process.
High-Pressure Steam
Steam produced at a pressure much higher than atmospheric pressure is referred to as high-pressure steam. Although the precise pressure that is deemed "high" can change depending on the situation, high-pressure steam is generally produced in industrial operations and power production at pressures greater than 15 psi (pounds per square inch), or 1.03 bar.
High-pressure steam has the following essential properties and uses:
Boiler Generation:
Specialized boilers made to withstand more significant pressures are frequently used to produce high-pressure steam. These boilers are used in power plants, factories, and other locations where steam with a high energy content is needed for various purposes.
Generation of Power:
High-pressure steam is essential for power plant steam turbine operation. Generators transform the mechanical work produced by the expansion of high-pressure steam in turbines into electrical power.
Industrial Procedures:
Many different industrial processes extensively use high-pressure steam. It is used in the manufacturing, petrochemical, and chemical industries for heating, sterilizing, and powering machinery.
Transfer of Heat:
The significant energy content of high-pressure steam makes it an efficient heat transmission medium. Heat exchangers transfer thermal energy to surfaces or fluids.
Combined Heat and Power, or cogeneration:
High-pressure steam is frequently used in cogeneration systems, which use the same energy source to produce both proper heat and electricity. The residual thermal energy can be transformed into electrical power, and the high-temperature steam can be utilized for industrial operations.
Heating in the District:
Specific district heating systems transmit heat for both residential and commercial heating needs using high-pressure steam.
Aspects of Safety and Quality to Consider:
Essential factors to consider include the quality and safety of high-pressure steam. Proper safety precautions, such as pressure relief systems, are crucial because steam at higher temperatures and pressures can result in more serious burns and injuries.
Design of Boilers:
High-pressure steam boilers must adhere to strict safety and engineering requirements. They are built using carefully chosen materials and structures to resist high temperatures and pressures.
The particular needs of the application frequently influence the use of high-pressure steam. For example, the use of high-pressure steam may be advantageous for processes that need high temperatures or high energy density. To guarantee efficiency and safety, systems handling high-pressure steam must be carefully designed and operated. High-pressure steam systems require constant maintenance, close observation, and adherence to safety regulations.
Turbine Blades
In gas turbines, steam turbines, and some kinds of water turbines, turbine blades are an essential part. In order to transform the kinetic energy of a flowing fluid—such as steam, gas, or water—into mechanical energy that can power a generator or carry out other tasks, these blades are essential. An outline of turbine blades and their purposes is provided below:
Function:
Turbine blades' main job is to extract energy from a high-velocity fluid (such as steam or gas) and transform it into rotating mechanical energy. Subsequently, this spinning energy powers a generator or other pieces of equipment.
Turbine Blade Types:
Depending on the particular needs and design of the turbine, there are various kinds of turbine blades. There are two typical kinds:
Impulse Blades: The impulse concept underlies the operation of these blades. The blades rotate because the high-velocity fluid (gas or steam) strikes them.
Reaction Blades: The impulse and reaction principles underlie the operation of these blades. The turbine is propelled by an impulse and a reaction force created by the fluid's expansion as it moves between the blades.
Design and Material:
Turbine blades are commonly made of high-strength materials that can tolerate high temperatures and mechanical stresses. Examples of everyday materials include high-alloy steels, superalloys, and cutting-edge materials like composites and ceramics. The blades' design is aerodynamically optimized to reduce losses and increase efficiency.
Systems for Cooling:
Cooling systems are frequently built into the turbine blades of gas turbines and some steam turbines, where temperatures can rise to extremely high levels. These mechanisms support the preservation of the blades' structural integrity and assist in avoiding overheating.
Profiles of Blades:
Specific aerodynamic profiles on turbine blades are intended to extract energy from the fluid effectively. In order to maximize the transformation of kinetic energy into mechanical energy, the blade's shape is essential.
Setting up:
Turbine blades are placed in rows to extract more energy from the fluid. A set of stationary blades (stator) and a set of spinning blades (rotor) make up each of the arrangement's possible stages.
Production Methods:
Turbine blades are frequently made by precision casting or machining to obtain the necessary forms and tolerances. This production procedure is essential to preserving the blades' aerodynamic effectiveness.
Repair:
Turbine blades experience a lot of stress when in use; thus, maintaining them properly is crucial to ensuring their longevity and performance. Turbine maintenance methods include routine inspections, repairs, and replacements if needed.
Turbine blades are essential parts for industrial, aviation, and power generation applications. The blades' design, composition, and state significantly impact the turbine's performance and efficiency. Developments in materials and production techniques are continuously enhancing the efficiency and dependability of turbine blades in a variety of applications.
Mechanical Work
High-pressure, high-temperature steam transforms thermal energy into mechanical energy, which powers a generator or carries out other mechanical tasks. This process is what gives a steam turbine its mechanical work. An outline of how a steam turbine produces mechanical work is provided below:
Water is heated in a boiler to produce steam. Nuclear reactions, burning fossil fuels (coal, natural gas, and oil), or employing renewable energy sources are some examples of heat sources.
Steam at High Pressure:
The boiler produces high-pressure, high-temperature steam, which carries considerable thermal energy.
Growth of the Turbine:
The steam turbine receives the high-pressure steam. The steam experiences expansion as it passes through the turbine blades. This expansion is a crucial step in transforming thermal energy into mechanical energy.
Blades of a turbine:
The turbine blades revolve due to the expansion of steam. Based on their operational principles, steam turbines can be divided into two primary categories: impulse turbines and reaction turbines. The blades in impulse turbines rotate because the high-velocity steam strikes them. Reaction turbines produce rotational motion by altering the steam's velocity and pressure as it moves through the blades.
The turbine shaft's rotation:
A shaft connects the revolving turbine blades. The shaft rotates as a result of the blades' revolution.
Connecting the generator:
A generator is attached to the turbine's shaft. The shaft's mechanical revolution turns the generator rotor within a magnetic field, causing an electric current to flow through the generator windings.
Electricity Production:
The power grid then distributes the electric current produced in the generator to residences, businesses, and other locations.
Condensation and Exhaust:
After passing through the turbine, the steam has a lower temperature and pressure. Subsequently, it is sent to a condenser in many power plants, where it condenses back into water. The condensed water is then sent back to the boiler for reheating and subsequent use in the steam cycle.
The turbine's design, the steam quality, and the control systems in place are some of the variables that affect a steam turbine system's overall efficiency. Thanks to advancements in control technology, materials, and turbine design, steam turbines used in power generation and industrial applications are now more dependable and efficient.
Expansion
In thermodynamics, expansion is the process through which a material changes volume in response to a rise in temperature or a fall in pressure. Different states of matter, such as gases, liquids, and solids, can all expand. I'll give a quick explanation of expansion in relation to gases and liquids here:
The expansion of gas:
When a gas's temperature rises, or the pressure falls, it expands. Gases' pressure and volume rise due to the molecules' increased kinetic energy and faster movement. The ideal gas law (PV = NRT), where P is pressure, V is volume, n is the number of moles of gas, R is the gas constant, and T is temperature, describes the relationship between pressure, volume, and temperature in a gas.
For instance, heating a gas contained in a container would raise the pressure inside the container, causing the gas to expand and take up more space.
Liquid Growth:
The leading cause of expansion in liquids is a rise in temperature. When heated, the molecules in a liquid gain energy, which makes them move more forcefully and increases the average distance between molecules. As a consequence, the liquid's volume increases.
The expansion of hot water is a typical illustration of liquid expansion. Water expands when heated, which may cause the fluid levels in containers to rise.
Solids' Thermal Expansion:
When a solid is heated, expansion takes place, which we call thermal expansion. A solid expands because its molecules vibrate more quickly when heated. The amount that a material expands or contracts for a specific temperature change is described by its coefficient of thermal expansion, which varies depending on the material.
When building, engineering, and designing structures and parts, the expansion and contraction of materials caused by temperature fluctuations are crucial factors to consider.
Numerous disciplines can benefit from expansion, and it's critical to consider these developments in practical applications. For example, engineers must consider the possibility of material expansion and contraction owing to temperature changes when designing bridges, buildings, and pipelines to avoid structural failure or damage. Analyzing gas expansion is also essential to comprehending thermodynamics and how heat engines, such as internal combustion engines and steam turbines, work.
Low-Pressure Steam
Steam produced or used at a pressure lower than atmospheric pressure is referred to as low-pressure steam. One crucial factor that influences the temperature, density, and energy content of steam is pressure. In many commercial, residential, and industrial settings where lower temperatures and pressures are appropriate, low-pressure steam is frequently used. The following are important details about low-pressure steam:
Range of Pressure:
Although the term "low-pressure" steam has no precise definition, it usually refers to steam produced at pressures lower than 15 pounds per square inch (psi) or 1.03 bar. However, the industry and application can affect the precise pressure range.
Uses:
There are several uses for low-pressure steam, such as but not restricted to:
Heating Systems: Low-pressure steam is utilized in building space heating systems, especially in older systems that use steam boilers.
Industrial Procedures: Steam is necessary for some industrial procedures to heat, humidify, or carry out particular manufacturing tasks. Low-pressure steam may be appropriate for some uses.
Food Processing: Low-pressure steam is frequently utilized in food processing to carry out operations like cooking, sterilization, and temperature control.
Energy Content and Temperature:
Steam's temperature and energy content are directly correlated with its pressure. Low-pressure steam will have a lower temperature than high-pressure steam. While it might not have as much energy per unit volume, it can nevertheless generate enough heat for a variety of uses.
Design of Boilers:
Compared to high-pressure boilers, boilers made to produce low-pressure steam may have various safety features and requirements. Preserving the necessary pressure and temperature for the intended use is one of the design considerations.
Safety Points to Remember:
Even while low-pressure steam typically poses fewer safety risks than high-pressure steam, appropriate safety precautions—such as pressure relief devices and routine maintenance—are still necessary to avoid mishaps and guarantee safe operation.
Handling condensate:
Condensate, or the liquid water created when steam releases its latent heat, is a common problem in low-pressure steam systems. Condensate handling must be done correctly to maintain system effectiveness and avoid water hammer.
Efficiency of Energy:
In some applications, using low-pressure steam can help save energy, mainly if the reduced pressure satisfies process requirements. The properties of the steam must be matched to the requirements of the particular application.
When deciding if low-pressure steam is appropriate, it is essential to comprehend the application's needs and features. Low-pressure steam is frequently employed in systems when its properties and energy requirements coincide with safety concerns.
Condensation
The process by which a substance transforms from a gas or Vapor to a liquid is called condensation. When the substance's temperature drops to the point where its vapor pressure matches the air pressure, a phase transition takes place. A frequent occurrence in nature, condensation finds extensive use in many different domains. Key elements of condensation are as follows:
Lowering the Temperature:
When a gas or Vapor is cooled, condensation occurs. The substance's molecular motion slows down when its temperature drops and the molecules combine to create a liquid.
The pressure of Vapor:
Vapor pressure affects the condensation process, which turns a gas into a liquid. The pressure that a vapor exerts while it is in equilibrium with its liquid phase is known as vapor pressure. Condensation happens when the air pressure and the vapor pressure are equal.
The state of the atmosphere:
A significant factor in condensation is atmospheric pressure. Although the pressure doesn't change as much as the temperature, condensation starts when a substance's vapor pressure equals the air pressure.
Dew Point:
The dew point is the temperature at which the air becomes saturated with moisture, and dew or frost starts to form. It is the location in the atmosphere where condensation takes place.
Dew Formation:
When damp air hits a surface that is colder than the air, dew forms, and water droplets form when the air's moisture condenses on the cooler surface.
Cloud Formation:
Condensation is a key mechanism in the creation of clouds in the atmosphere. Clouds are formed when warm, humid air rises and comes into contact with cooler air at higher elevations. The water vapor in the warm air condenses to produce visible water droplets.
In industrial processes, condensation:
Condensation is used in many industrial operations. For instance, compressed gas is allowed to expand in air conditioning and refrigeration systems, causing the refrigerant to cool and condense.
Heat exchanger applications:
Heat exchangers employ condensation to move heat from a vapor to a liquid state. Power plants, industrial operations, and HVAC systems all frequently use this procedure.
Inverse Procedure:
Evaporation is the opposite of condensation and occurs when heat is absorbed by a liquid, turning it into a gas or Vapor.
Avoiding Condensation:
Condensation can be controlled by regulating temperature and humidity levels and employing insulation to keep surfaces from cooling below the dew point.
Condensation is critical to comprehending and managing everything from industrial processes and HVAC system design to weather patterns and climate research. Controlling condensation is essential to avoiding problems such as corrosion, water damage, and ice formation in various applications.
Blades and Rotors
Blades and rotors are essential parts of a steam turbine's ability to transform thermal energy from steam into mechanical energy. An outline of a steam turbine's rotors and blades is provided below:
Blades
Turbine blades:
Function: Turbine blades are the main parts responsible for drawing energy from high-pressure, high-temperature steam and turning it into mechanical energy.
Types:
Impulse Blades: Use the steam's impact on the blades to transform the kinetic energy of high-velocity steam into mechanical energy.
Reaction Blades: These blades work on the impulse and reaction principles. As steam moves through them, it expands, producing pressure-driven and kinetic forces.
Blade Profiles:
In order to effectively harness the energy of the steam flow, turbine blades are engineered with particular aerodynamic profiles. In order to maximize energy extraction and minimize losses, the blades' form is essential.
Materials:
Blades are usually made of high-strength materials that can bear mechanical pressures and high temperatures. Advanced materials, high-alloy steels, and superalloys are frequently utilized.
Cooling Mechanisms:
Some steam turbines, particularly those found in power plants with high temperatures, may include cooling systems built into the turbine blades to avoid overheating and preserve structural integrity.
Rotors
Turbine Rotor:
Function: The steam turbine's rotor, to which the turbine blades are attached, is its rotating part. It is in charge of turning the blades' rotational motion into mechanical labor.
Connection to Shaft: The rotor is attached to the turbine's shaft. As a result of the steam impact, the rotor revolves in tandem with the turbine blades, sending mechanical energy to the shaft.
Design of the Rotor:
The rotor's design is essential for the steam turbine to operate effectively and efficiently overall. It must be able to endure the mechanical strains brought on by the high-speed steam flow and blade rotation.
Seals and Bearings:
The bearings supporting the rotor make smooth rotation possible. Seals also reduce steam leakage and preserve turbine efficiency.
Maintaining equilibrium:
The rotor must be adequately balanced to avoid vibration and guarantee the steam turbine's steady and dependable operation. Rotor imbalance can result in reduced efficiency and mechanical problems.
Resources:
Rotor materials need to be robust and resistant to fatigue—several variables, including the turbine's operating circumstances and design criteria, influence material selection.
The core of a steam turbine is made up of the rotor and turbine blades, where thermal energy is transformed into mechanical work. This mechanical labor powers a generator, generating electricity in power plants or carrying out other mechanical tasks in a variety of industrial settings. The design, construction, and upkeep of these vital parts significantly impact the steam turbine's dependability and efficiency.
Turbine Blades
In turbines, which are machines that transform the energy of a flowing fluid (such as steam, gas, or water) into mechanical energy, turbine blades are essential parts. Power generation, aviation, and industrial processes are just a few of the many uses of turbines. In this energy conversion process, turbine blades are essential. The following are important features of turbine blades:
Function
Extracting Energy:
Turbine blades capture energy from the kinetic energy of flowing water or a high-velocity fluid (such as steam or gas). As a result of the energy extraction, the blades rotate.
Mechanical Tasks:
The turbine blades do mechanical work as they rotate. In industrial processes, this rotational motion can be utilized to generate electricity, power a generator, or carry out other mechanical tasks.
Turbine Types:
Different types of turbines require different turbine blades.
Steam turbines: High-pressure, high-temperature steam is converted into electricity by the turbine's blades.
Gas Turbines: High-velocity gases from combustion power the blades of gas turbines.
Hydraulic Turbines: These devices use water movement to generate energy through their blades.
Characteristics
Design of Aerodynamics:
Specific aerodynamic profiles of turbine blades are intended to capture fluid energy effectively. The blades' form is essential to maximizing energy extraction and minimizing losses.
Resources :
Turbine blades are commonly made from materials that can tolerate high temperatures, mechanical loads, and corrosion. Examples of everyday materials include high-alloy steels, superalloys, and cutting-edge materials like composites and ceramics.
Cooling Mechanisms:
Turbine blades may have cooling systems to prevent overheating and preserve structural integrity in applications with extremely high temperatures, such as gas turbines or specific parts of steam turbines.
Mounting and Roots:
The portion of the turbine blade that fastens to the rotor is called the root. The blade attachment on the rotor needs to be sturdy to endure the mechanical stresses during rotation.
Types of Turbine Blades
Impulse Blades:
Impulse blades work by transforming a high-velocity fluid's kinetic energy into mechanical energy by the fluid's impact on the blades. Impulse turbines frequently have these blades.
Blades of Reaction:
Impulse and reaction are the two guiding concepts of reaction blade operation. As the fluid moves between the blades, it expands, producing forces caused by pressure as well as kinetics. Reaction turbines frequently use reaction blades.
Maintenance
Maintaining equilibrium:
To avoid vibration and guarantee the turbine's steady and dependable performance, the blades must be properly balanced.
Examining and fixing:
Turbine blades must undergo routine examinations and, if necessary, repairs or replacements to preserve efficiency and avoid unplanned failures.
Turbine blades are an essential component of energy conversion systems. They are precisely engineered to optimize efficiency and dependability in a range of applications. Design and material advancements continuously enhance the performance of turbine blades in contemporary turbines.
Blade Profile
The blade profile, also known as the airfoil profile or blade shape, refers to the cross-sectional shape of a turbine or aircraft blade as seen from the direction of fluid flow (such as air or steam). The design of the blade profile is crucial for optimizing the aerodynamic performance of the blade and, consequently, the efficiency of the entire system. Here are key aspects of blade profiles:
Characteristics
Efficiency of Aerodynamics:
The main objective of developing a particular blade profile is high aerodynamic efficiency. This entails increasing lift, reducing drag, and guaranteeing even airflow across the blade surface.
Drag and Lift:
The blade profile's ability to produce lift—necessary for supplying lift in aircraft or extracting energy in turbines—is determined by its form. Additionally, the profile is made to minimize drag because too much drag can hinder performance.
The angle of Attack:
The angle formed by the chord line—a straight line that joins the blade's leading and trailing edges—and the fluid flow direction is known as the angle of Attack. The blade profile is meticulously engineered to maximize the angle of Attack for various operating situations.
Chord Length:
The distance along the chord line between the leading and trailing edges is known as the chord length. Chord length and shape are characteristics of blade profiles that affect the blade's overall performance.
Common Blade Profiles
Profiles of NACA Airfoils:
A set of airfoil profiles with standardized numbering was created by the National Advisory Committee for Aeronautics (NACA). Applications for NACA airfoils in turbomachinery and aircraft are numerous.
Symmetric and Asymmetric Profiles:
Specific blade profiles have identical top and lower surfaces, which is known as symmetry. Others have varied shapes on the upper and bottom surfaces, making them asymmetrical. Certain aerodynamic constraints frequently call for the adoption of asymmetric profiles.
Cambered Profiles:
The curve of the blade's upper and lower surfaces is known as camber. Cambered profiles improve overall performance by creating lift even at zero angle of Attack.
Twisted Profiles:
In some applications, like airplane propellers, blade profiles may be twisted over their length to maximize performance across various blade portions.
Applications
Aircraft Wings:
Aerial wings employ particular airfoil profiles to provide lift and control. The design of the wing profiles is essential for the airplane's aerodynamic performance.
Turbine blades:
Turbine blades in gas turbines, wind turbines, and steam turbines employ precisely engineered profiles to effectively extract energy from the fluid (steam, gas, or wind).
Propeller blades:
Specialized profiles are used by propeller blades in aircraft propulsion systems or marine applications to generate thrust effectively.
Fan Blades:
For the best airflow and energy efficiency, fan blades in industrial fans or HVAC systems require particular profiles.
Computational Fluid Dynamics (CFD)
Analysis and Simulation:
Before building physical prototypes, engineers can use advances in Computational Fluid Dynamics (CFD) to model and study the performance of various blade profiles under multiple situations.
The application, operating environment, and required performance attributes all influence the choice of blade profile. Engineers optimize blade profiles for particular uses using advanced design and analytical methods, guaranteeing effectiveness and dependability in a range of applications.
Materials
In order to survive the severe circumstances of high temperatures, pressures, and mechanical stresses found in turbine applications, the materials used to make turbine blades are carefully selected. Depending on their working conditions, various turbine types—such as wind, gas, and steam turbines—may need particular materials. The following materials are frequently found in turbine blades:
Superalloys
Uses: Steam turbines, gas turbines
Properties:
Strength at high temperatures and resistance to creep
outstanding resistance to corrosion.
Frequently include cobalt, nickel, and other alloying metals.
Able to tolerate significant variations in temperature.
Single-Crystal Alloys
Uses: Aircraft engines and gas turbines
Properties:
A uniform crystal structure provides superior high-temperature strength.
Improved ability to withstand heat fatigue.
Utilized in turbines' hotter regions.
Ceramic Matrix Composites (CMCs)
Uses: High-temperature settings and gas turbines
Properties:
Outstanding chemical and thermal stability.
High strength at high temperatures.
Lighter than alloys made of metal.
Ideal for turbine components with high temperatures.
Titanium Alloys
Uses: Some gas turbines and aircraft engines
Properties:
High ratio of strength to weight.
Strong resistance to corrosion.
Utilized in turbine areas where reduced weight is essential.
Nickel-Based Alloys
Uses: Steam turbines, gas turbines
Properties:
Strong at high temperatures.
Impervious to corrosion.
It is ideal for turbine areas with high temperatures and pressures.
Coating Materials
Uses: Steam turbines, gas turbines
Properties:
High temperatures are protected from using thermal barrier coatings (TBCs).
Oxidation-resistant coatings increase the blades' lifespan.
Coatings can be used to improve performance and durability.
Composite Materials
Uses: Wind Generators
Properties:
The materials employed are carbon fiber, fiberglass, or hybrid composites.
Resistance to fatigue, low weight, and high strength.
Frequently utilized in wind turbine blade fabrication.
High-Strength Steels
Some Industrial Turbine Applications
Properties:
High durability and strength.
Used in situations where resistance to high temperatures is not the primary consideration.
Considerations for Material Selection
Pressure and Temperature:
The materials must tolerate the high temperatures and pressures required for the turbine's operating conditions.
Resistance to Corrosion:
Materials that are resistant to corrosion are essential, particularly in steam turbines with moisture.
Resistance to Fatigue:
Because turbine blades are subjected to cyclic loads, fatigue-resistant materials are essential to guarantee long-term dependability.
Weight-related considerations:
Lightweight materials like titanium alloys are used in aviation engines and some gas turbines to reduce weight and increase fuel efficiency.
Production Methods:
The turbine blade manufacturing procedures, such as casting or precision machining, may influence the choice of material.
Developments in Materials:
Research and developments in materials science are creating new alloys and composites with better qualities.
A crucial component of turbine design is the choice of materials for the blades, which guarantees that they can endure harsh environments and deliver dependable and effective performance for the duration of their useful lives.
Mechanical Work
High-pressure, high-temperature steam carries thermal energy, which is transformed into rotating mechanical energy by a steam turbine. After that, this mechanical energy is used to power a generator, which generates electricity, or to carry out other mechanical tasks. Numerous essential steps make up the process by which a steam turbine produces mechanical work:
In a boiler, water is heated with a heat source to produce steam. This heat source may originate from nuclear processes, the burning of fossil fuels (oil, coal, and natural gas), or other sources.
Steam at High Pressure:
The boiler produces high-pressure, high-temperature steam. There is a lot of thermal energy in this high-pressure steam.
Growth of the Turbine:
The steam turbine receives the high-pressure steam. The steam experiences expansion as it passes through the turbine blades. In order to transform the steam's thermal energy into mechanical energy, this expansion is necessary.
Blades of a turbine:
The turbine blades revolve due to the expansion of steam. Based on their operational principles, steam turbines can be divided into two primary categories: impulse turbines and reaction turbines. Reaction turbines use both impulse and reaction forces as steam expands through the blades, whereas impulse turbines use the impact of high-velocity steam on the blades.
The turbine shaft's rotation:
A shaft connects the revolving turbine blades. The shaft rotates as a result of the blades' revolution.
Connecting the generator:
A generator is attached to the turbine's shaft. The shaft's mechanical revolution turns the generator rotor within a magnetic field, causing an electric current to flow through the generator windings.
Electricity Production:
The power grid then distributes the electric current produced in the generator to residences, businesses, and other locations.
Condensation and Exhaust:
After passing through the turbine, the steam has a lower temperature and pressure. Subsequently, it is sent to a condenser in many power plants, where it condenses back into water. The condensed water is then sent back to the boiler for reheating and subsequent use in the steam cycle.
The turbine's design, the steam quality, and the control systems in place are some of the variables that affect a steam turbine system's overall efficiency. Thanks to advancements in control technology, materials, and turbine design, steam turbines used in power generation and industrial applications are now more dependable and efficient. The mechanical effort produced by steam turbines is one essential component of turning heat into usable energy for a variety of uses.
Exhaust
The term "exhaust" describes the outlet or discharge of the working fluid (steam, gas, or air) following its passage through the turbine and completion of work in a steam turbine or other heat engine. Because it completes the energy conversion process and gets the working fluid ready for the subsequent cycle, the exhaust stage is an essential component of the thermodynamic cycle. The following are important details about the exhaust stage:
Reduced Temperature and Pressure:
The working fluid's temperature and pressure drop as it moves through the turbine and does mechanical work. The fluid's temperature and pressure are lower at the exhaust stage than they were before entering the turbine.
Speed of Exit:
At the exhaust stage, the fluid frequently has a high velocity as it exits the turbine. The fluid's expansion causes this as it moves past the turbine blades. For some uses, like wind power or jet propulsion, the high-speed exhaust flow can be captured.
Steam Turbine Condensation:
The exhaust steam from steam turbines is usually sent to a condenser, a heat exchanger. The condenser condenses the steam back into liquid water when it takes heat from it. Subsequently, this condensed water is returned to the boiler for warming, completing the steam cycle.
Gas turbines for recompression:
Compressors are devices that may receive the exhaust gases from gas turbines. Before the exhaust gases are released into the atmosphere, they are compressed by the compressor. This recompression may improve the gas turbine system's total efficiency.
Aspects of the Environment:
The composition of the exhaust (such as in the case of gas turbines) is of environmental concern. The emissions from the exhaust may include pollutants, and efforts are made to minimize environmental impact through technologies like exhaust gas treatment systems.
Propulsion by Jets:
Exhaust from jet engines is released quickly to provide thrust, which is necessary to move cars and other vehicles forward.
Recovery of Waste Heat:
Some systems use exhaust waste heat recovery to increase overall efficiency. Heat exchangers can capture and use the thermal energy in the exhaust for other purposes.
Cycle:
In the thermodynamic process, one cycle ends in the exhaust stage. The working fluid is prepared to be reintroduced into the system to start a new cycle after expelling some of its energy to accomplish work.
The exhaust stage must be understood and optimized for a heat engine or turbine system to operate as efficiently as possible. The particular application—power generation, propulsion, or industrial processes—determines the exhaust design considerations.
It is important to remember that boilers come in various forms, each with a unique use and design. A number of variables, including the intended use of steam, fuel availability, and efficiency concerns, influence the type of boiler selected.
A basic operation in numerous industries, steam generation is essential to manufacturing, power generation, and heating applications all over the world.
Types of Steam Turbines
Steam turbines come in various varieties, such as:
Impulse Turbines: These turbines work by directing high-velocity steam jets onto the turbine blades using the impulse principle.
Reaction Turbines: Steam expands as it moves over and past the blades in these turbines, which work on the impulse and reaction principles.
Steam turbines are essential parts of power plants, where they frequently work in tandem with other systems to produce energy. For more than a century, they have been a necessary technology for power generation, and they still contribute significantly to the global production of energy.
Compact steam turbines have numerous applications, including mechanical drives in industrial machinery and power generation in small-scale power plants. A steam turbine is a device that transforms steam's thermal energy into mechanical energy. Power from small steam turbines usually ranges from a few kilowatts to many megawatts.
Small steam turbines are usually designed with multiple stages of blades that expand steam to provide rotational force. Usually mounted on bearings, the steam turbine rotor revolves on a shaft. The turbine's rotor rotates because the steam is directed onto the blades by nozzles. The rotating force is transferred to a generator or other apparatus to generate mechanical power or electricity.
Numerous businesses, including the food processing, chemical, and pharmaceutical sectors, use small steam turbines. They power pumps, compressors, fans, and other machinery and equipment. They are also employed in combined heat and power (CHP) systems, which use steam from a boiler to power a steam turbine, producing heat and electricity for industrial operations.
Steam Turbine Advantages
Two benefits of tiny steam turbines are reliability and good efficiency. Additionally, they may run on a range of fuels, such as natural gas, coal, and oil. Small steam turbines may also be made to run at different loads, which means they can be used in a variety of settings.
However, the use of small steam turbines has certain drawbacks. They can be costly to run and maintain, and they need routine maintenance to function at their best. Furthermore, a steam turbine may have a significant initial capital cost.
In conclusion, various sectors rely on modest steam turbines as a significant source of mechanical energy and power. Due to their excellent efficiency and dependability, they are appropriate for a variety of applications. However, they can be costly to run and maintain and require routine upkeep.
Today's process plants, pharmaceutical companies, mining interests, and a wide range of other users—including, of course, the petroleum, petrochemical, and chemical-process industries—rely heavily on the dependability and variety of equipment.
The economy needs longer, and longer intervals between overhauls, operating pressures, and temperatures are continuously increasing, single-train capacities are expanding rapidly, and continuity of service becomes increasingly important. The process industries rely on steam turbines as dependable partners. They have demonstrated their fundamental dependability and are now showing new adaptability by meeting all demands for increased capacity, speed, and reliability.
There are more mechanical drive turbines in the process industries everywhere you turn, and each year, horsepower and speed increase. Additionally, new steam turbines are incorporating technical advancements everywhere you look. Numerous manufacturers merit praise for their proficiency in resolving the more challenging steam turbine application issues.
In the final quarter of this century, engineers have developed a whole new generation of turbines—machines with sizes and speeds that were only conceivable a few decades ago—through meticulous examination, innovative research, perseverance, and advanced planning. Among the technologies that contributed to this advancement were cam-operated valve gear and controls, solid rotors, highspeed bearings, taller last-stage blades (sometimes known as "buckets"), multi-flow exhausts, and other highly complex control systems and computerized designs.
An extensive range of single or multivalve steam end designs are available from knowledgeable manufacturers to satisfy any particular pressure and temperature requirements. A straightforward, single-casing steam turbine is used in the vast majority of industrial and cogeneration systems intended to generate electricity. These turbines (Fig. 1.1) can be made to offer operational flexibility so that steam from various sources can be used economically to supply:
Compressors, pumps, and other driven equipment can be powered directly or through a gearbox.
Steam at the amounts and pressures needed for lower-pressure turbines or integrated processes
The desired electric power
Selling cogenerated energy to the neighborhood utility
Overview of Steam Turbine
Fundamentals
Let's review how a steam turbine transforms steam's thermal energy into usable work before moving on to turbine selection. As steam expands from intake to exhaust pressure, a turbine's nozzles, and diaphragms are made to guide the flow of steam into well-formed, fast-moving jets. These jets strike the rotor's rotating rows of blades. The steam's kinetic energy is transformed into the shaft's rotational energy by the blades.
Reaction and impulse turbines are the two main varieties. Steam expands in both the stationary and moving blades of a reaction turbine. The stationary blades' steam jet energy is harnessed by the moving blades, which also function as nozzles. Since they are moving nozzles, the pressure drop across them creates a reaction force that balances the stationary blades' steam jet force. Rotation is the result of these combined forces.
The reaction turbine's design must reduce leakage around the rotating blades in order to function effectively. Making the majority of internal clearances relatively minor does this. Due to the high thrust loads produced, the reaction turbine typically needs a balancing piston, much like those seen in big centrifugal compressors. Despite its often better starting efficiency, the reaction turbine is rarely employed for a mechanical drive in the United States due to these factors. Nevertheless, Europe and the rest of the world employ reaction turbines extensively.
They are worthy of discussion and will be addressed at a later time. The pressure drop across the moving blades of an impulse turbine is minimal or nonexistent. When the steam jets hit the rotating blades, all of the steam energy is delivered to the rotor.
Steam Turbine Description and Components
A steam turbine is a machine that transforms pressurized steam's thermal energy into mechanical work. This particular kind of heat engine works by changing the energy found in high-pressure steam into a rotating motion.
A steam turbine's fundamental parts are as follows:
Rotor: The revolving component of the turbine that transforms the kinetic energy of the steam into mechanical work is called the rotor. Usually, a central shaft holds several blades or buckets.
Stator: The stator is the turbine's stationary component with fixed nozzles or blades. It provides the required direction and control by directing the steam flow onto the rotor blades.
Steam intake: High-pressure steam enters the turbine through the steam intake. A steam source, like a boiler, is connected to it, and the steam is sent into the turbine to expand.
Exhaust Outlet: After working, the low-pressure steam leaves the turbine through the exhaust outlet. Usually, a condenser or other steam utilization equipment is attached to it.
Governor: The governor is a control device that keeps the turbine running steadily by controlling the steam flow and maintaining a steady speed.
Power stations frequently use steam turbines to produce electricity. Based on their design and functional properties, they can be divided into various varieties, including impulse or reaction turbines, condensing or non-condensing turbines, and single-stage or multi-stage turbines.
Steam pressure and temperature, turbine design, and operating circumstances are some of the variables that affect a steam turbine's efficiency. Steam turbines can attain high-efficiency levels, particularly in combined cycle power plants where the turbine's waste heat is recovered and used to produce more electricity.
Due to their dependability, scalability, and capacity to employ a range of fuel sources, including fossil fuels and renewable energy sources like biomass or geothermal steam, steam turbines have generally been utilized extensively for power generation.
Rotor
One essential part of a steam turbine is the rotor. The turbine's rotating component transforms the steam's kinetic energy into mechanical work. Usually, the rotor consists of several blades or buckets linked to a central shaft.
The rotor's primary job is to draw energy from the steam that passes through the turbine at high temperatures and pressures. The rotor rotates because of the force that the steam exerts on the blades as it passes over them. Mechanical effort that can be utilized for a number of purposes, including power plant energy generation and industrial machinery drive, is produced by the rotation of the rotor.
The rotor's design and construction are essential for the steam turbine to operate effectively and dependably. The blades or buckets' form is designed to improve energy transfer and steam flow. They are also specifically designed to endure extreme pressures, temperatures, and centrifugal forces.
The rotor's configuration might vary depending on the steam turbine's size and kind. Impulse turbine blades are oriented either axially or radially, and the steam acts on them in distinct phases. Reaction turbine blades are designed to react to the steam as it flows over them continuously.
The turbine drives a generator or mechanical load that is connected to the rotor. Through a gearbox or connection, the rotor's rotational motion is transferred to the generator or load, where it is transformed into mechanical work or electrical power, respectively.
A steam turbine's entire performance and output depend heavily on its rotors, which must be well-designed and efficient. To ensure they can endure the operating circumstances and provide the required power output while retaining dependability and durability, they undergo a thorough engineering study and testing process.
Stator
Another crucial part of a steam turbine is the stator. It is the stationary component that encircles the turbine's rotor. As the steam travels through the turbine, the stator is in charge of guiding and managing its flow, transforming the steam's kinetic energy into mechanical work.
The stator's main job is to house the vanes or stationary blades that direct the steam flow onto the rotor blades. These stationary blades optimize the steam flow, guaranteeing effective energy transmission and maximum power output. The stator blades are usually inclined or curved to keep the steam flowing uniformly and in the proper direction.
The stator supports and shields the rotor and other internal turbine parts, directing the steam flow. It also helps keep the rotor and stator blades aligned and offers structural stability.
The stator is usually built using premium materials that can tolerate the high pressures, temperatures, and mechanical stresses found in a steam turbine. Steel or other alloys with superior mechanical and heat-resistant qualities are frequently used.
The stator of large steam turbines consists of several parts, or stages, each with a set of stationary blades. These phases are intended to increase the system's overall efficiency by gradually drawing energy from the steam as it travels through the turbine.
An essential component of the steam turbine, the stator transforms steam energy into mechanical work by cooperating with the rotor. Together, they provide a very dependable and efficient power generation system that is utilized in a variety of industries, such as refineries, power plants, and industrial operations.
Steam Inlet
High-pressure steam enters the steam turbine through the steam intake, sometimes referred to as the steam admission or steam entry. It is an essential part that enables steam to enter the turbine and start the process of producing electricity.
Usually found on the turbine's outside, the steam inlet is attached to the steam source, which could be a boiler or steam generator. At a certain angle and speed, the high-pressure steam enters the turbine through the steam inlet.
To enable effective and controlled entry of steam into the turbine, the steam intake is built with several elements. These include:
Nozzles: The steam inlet may feature a series of nozzles or guide vanes to help regulate the flow direction and velocity of the steam entering the turbine. Because they are adjustable, these nozzles may be positioned to maximize the efficiency of the steam flow.
Steam Strainers: Steam strainers or filters are occasionally placed at the steam entrance to eliminate solid particles or contaminants from the steam. These strainers help prevent damage to the turbine blades and guarantee their smooth operation.
Steam Control Valves: Steam control valves are frequently placed near the steam inlet to control the flow of steam into the turbine. These valves can change the steam's flow rate and pressure, allowing the turbine's power output to be precisely controlled.
Expansion Joints: Expansion joints are utilized at the steam inlet to allow for the turbine components' thermal expansion and contraction. They permit the required movement brought on by temperature changes while assisting in preserving the integrity of the turbine casing.
The design and arrangement of the steam inlet may change depending on the size and kind of steam turbine. The objective is to reduce pressure losses, guarantee adequate steam flow, and shield the turbine from any possible harm.
The steam inlet is essential to the functioning of the steam turbine since it permits high-pressure steam to enter the turbine and starts the energy conversion process. Its functionality and design are critical for maximizing turbine performance and guaranteeing dependable power production.
Exhaust Outlet
After the steam or gas has passed through the turbine and done its job, it exits through the exhaust outlet, sometimes referred to as the exhaust nozzle or exhaust diffuser. Because it enables the safe and effective disposal of spent steam or gas, the exhaust outlet is a crucial part of a steam turbine system.
The exhaust exit is usually found at the other end of the turbine from the steam or gas inlet. Before being released into the environment or used for different purposes, such as heating or industrial activities, it is intended to transform the high-velocity, high-pressure steam or gas into a lower-velocity, lower-pressure state.
The exhaust outlet serves a number of vital purposes, including:
Pressure Reduction: The exhaust outlet is made to progressively lower the pressure of the gas or steam as it expands and passes through the turbine. This reduces the pressure at which the gas or steam leaves the turbine, reducing the possibility of abrupt pressure changes that could harm the turbine or related machinery.
Energy Recovery: The turbine system's overall efficiency is increased when the exhaust outlet is connected to a condenser or heat recovery system. This system recovers heat or transforms it into useful power, thereby extracting more energy from the exhaust steam or gas.
Noise reduction: To comply with noise restrictions and provide a more peaceful working atmosphere, the exhaust outlet's design may include features like diffusers or silencers to lessen noise produced by the high-velocity exhaust steam or gas.
The exhaust outlet's precise design and arrangement may change depending on the steam turbine's size, kind, and intended use. The design takes into account variables like temperature, flow rate, and exhaust pressure to maximize turbine performance and guarantee safe operation.
The exhaust outlet, which is in charge of securely and effectively releasing the wasted steam or gas, is an essential part of a steam turbine system. Its design seeks to regulate noise, pressure, and velocity while permitting energy recovery when appropriate.
Governor of the Steam Turbine
In steam turbines, the governor is a crucial control mechanism that manages the turbine's speed and power output. Its primary purpose is to keep the turbine's rotational speed within a predetermined range, independent of variations in the load or steam conditions.
Based on the feedback control principle, the governor continuously checks the turbine's speed and modifies the steam flow to keep it at the target speed. Here is a quick rundown of the governor's operations:
Speed Sensing: The governor has devices that measure the turbine's rotational speed, such as magnetic pickups or centrifugal weights. The governor control system receives input information from these sensors.
Control System: After processing the speed signals, the governor control system compares them to the target speed setpoint. It computes the discrepancy between the setpoint and actual speed and establishes what has to be changed.
Steam Flow Regulation: The governor control system modifies the steam flow rate entering the turbine in response to the error signal. Usually, this is accomplished by adjusting the steam control valves that govern the steam flow. The governor raises the steam flow when the turbine speed is below the setpoint and lowers the steam flow when the speed is above the setpoint.
Feedback Loop: To maintain the desired speed, the governor continuously modifies the steam flow based on its monitoring of the turbine speed. It functions as a closed-loop feedback system, changing the steam flow in response to a comparison between the observed speed and the setpoint.
The governor keeps the steam turbine running steadily by adapting to variations in load demand and preserving a steady speed. It assists in avoiding situations of excessive or insufficient speed that can harm the turbine or result in problems with operation. The governor also offers a way to regulate the turbine's output power, enabling it to react to modifications in the electrical grid or other demands on the power system.
Advanced electronic or digital governor systems, which provide more accurate control and flexibility, are frequently used in modern steam turbines. To integrate into larger control systems, these systems may also include extra features such as communication interfaces, protective measures, and load sharing among several turbines.
The governor is essential to the safe and effective operation of steam turbines. It controls the turbine's speed and power output to achieve the required operating parameters.
Steam Turbine Application Areas
Steam turbines are used in a wide variety of applications, including:
Power generation: The steam turbine is the most popular prime mover used in power plants to produce energy. Additionally, they make both heat and electricity in combined heat and power (CHP) facilities.
Industrial operations: Steam turbines power compressors, pumps, and other equipment in various industrial operations, including the production of paper, chemicals, and oil.
Marine propulsion: Big ships like cruise ships and aircraft carriers are propelled by steam engines.
Transportation: Some locomotives and other rail vehicles are powered by steam turbines.
Here are some particular instances of the various industries that use steam turbines:
Power generation: Steam turbines drive generators in the power generation sector to create electricity. Usually, a boiler heated by burning nuclear or fossil fuels produces steam. The steam propels the turbine blades, which turn the generator shaft. A rotor attached to the generator shaft revolves to produce power.
Industrial processes: Steam turbines power compressors, pumps, fans, and other equipment in the industrial process sector. They also produce heat for operations like liquid distillation and product drying.
Marine propulsion: Large ships like cruise ships and aircraft carriers are powered by steam turbines in the marine propulsion sector. The boat moves over the water thanks to propellers that are powered by steam turbines.
Transportation: Steam turbines power some locomotives and other rail vehicles in the transportation sector, and some electric power plants are constructed on trains.
The steam turbine is an efficient and adaptable prime mover that may be utilized in many different applications. It is an essential part of the electricity infrastructure around the world.
Power Generation with Steam Turbines
Power plants use steam turbines, which transform the thermal energy of steam into mechanical energy, to produce electricity. In a boiler, steam is produced by heating water using nuclear power, fossil fuels, or renewable energy sources like geothermal or solar power. After that, the steam turbine receives the high-pressure steam, which expands and powers the turbine blades. In order to generate electricity, a generator is rotated by the turbine blades attached to a shaft.
There are two main types of steam turbines used in power generation:
Condensing turbines: The most prevalent kind of steam turbine found in power plants is a condensing turbine. They work by letting the steam that leaves the turbine condense back into water, allowing the turbine to run more efficiently.
Backpressure steam turbines: In combined heat and power (CHP) facilities, backpressure steam turbines produce heat in addition to electricity. They work by removing a portion of the turbine's steam before it has had a chance to expand ultimately. After that, this steam is used to heat buildings or industrial operations.
Steam turbines are an effective and dependable method of producing electricity. They may be used to produce electricity from a range of energy sources and are also incredibly adaptable.
Boiler: The boiler produces steam by heating water.
Superheater: This device raises the temperature of the steam.
Reheater: The steam expands via the high-pressure turbine and is then heated in the reheater.
High-pressure turbine: A portion of the steam's energy is extracted by the high-pressure turbine.
Low-pressure turbine: This device uses the steam's residual energy to generate electricity.
Steam is converted back into water by the condenser.
Condensed water is pumped back to the boiler by the feedwater pump.
Generator: The turbine shaft's mechanical energy is transformed into electrical power by the generator.
Steam turbines are an essential component of the worldwide energy infrastructure. Since they may produce power from a range of renewable energy sources, they are an integral part of the shift to a clean energy future.
Industrial Processes Where Steam Turbine is Used
Numerous industrial processes make use of steam turbines, such as:
Oil refinery: Steam turbines power compressors, pumps, and other equipment in oil refineries and produce heat for distillation procedures.
Chemical processing: Steam turbines power compressors, pumps, and other equipment in chemical facilities and produce heat for chemical reactions.
Papermaking: Pulpers, paper machines, and dryers are among the equipment in paper mills powered by steam turbines. They also provide heat to dry paper.
Food and beverage processing: Conveyors, mixers, and cookers are among the equipment in food and beverage processing facilities that are powered by steam turbines. Additionally, they are employed to produce heat for pasteurization and sterilization procedures.
Textile manufacturing: Spinners, weavers, and finishers are among the equipment in textile mills powered by steam turbines. Additionally, they produce heat for textile dyeing and drying.
Metalworking: Rolling mills, presses, and saws are among the equipment in metalworking operations that are powered by steam turbines. Additionally, they are employed to produce heat for heat treatment procedures.
The following are particular instances of the various industrial operations that employ steam turbines:
Oil refining: Steam turbines power compressors in the oil refining sector, which compress crude oil to high pressures. Following compression, the oil is sent into distillation columns, where it is split into several fractions, including jet fuel, diesel fuel, and gasoline. Additionally, steam turbines provide heat for distillation procedures and power pumps that move oil around the refinery.
Chemical processing: In the chemical processing sector, steam turbines power compressors that compress gases like air, nitrogen, and hydrogen. The compressed gases are then employed in a number of chemical reactions, including the creation of fertilizer and ammonia. In addition to producing heat for chemical reactions, steam turbines are utilized to power pumps and mixers.
Papermaking: Pulpers that convert wood chips into fibers are powered by steam turbines in the papermaking sector. The fibers are combined with chemicals and water to create a slurry, which is then put into a paper machine. After the slurry is formed into a sheet of paper by the paper machine, it is dried and completed. All of the equipment in a paper mill is powered by steam turbines, which also produce heat for paper drying.
Food and beverage processing: Conveyors that move food and beverage items through the processing facility are powered by steam turbines in the food and beverage processing sector. They also produce heat for pasteurization and sterilization procedures, as well as power mixers and cookers.
Textile manufacturing: Steam turbines propel spinners that create yarn from fibers in the textile manufacturing sector. The yarn is then passed to a weaver, who completes the fabric. All of the equipment in a textile mill is powered by steam turbines, which also produce heat for textile dyeing and drying.
Metalworking: Steam turbines power rolling mills, which form metal sheets and plates into various shapes. They also power metal-cutting saws and presses, which punch or stamp metal components. All of the equipment in a metalworking shop is powered by steam turbines, which also produce heat for heat treatment procedures.
Steam turbines are vital to many industrial operations. They offer a dependable and effective means of producing heat and powering equipment.
Marine propulsion with Steam Turbines
For more than a century, steam turbines have been employed for naval propulsion. In the early 20th century, they dominated marine propulsion, but diesel engines have since mostly supplanted them. Nonetheless, certain significant ships, like cruise ships and aircraft carriers, continue to employ steam turbines.
Due to their dependability and efficiency, steam turbines are an excellent option for marine propulsion. They are also capable of producing a lot of power, which is necessary for big ships. However, the construction and maintenance of steam turbines are incredibly costly and complex.
Boiler: The boiler produces steam by heating water.
Superheater: This device raises the temperature of the steam.
Reheater: The steam expands via the high-pressure turbine and is then heated in the reheater.
High-pressure turbine: A portion of the steam's energy is extracted by the high-pressure turbine.
Low-pressure turbine: This device uses the steam's residual energy to generate electricity.
Steam is converted back into water by the condenser.
Condensed water is pumped back to the boiler by the feedwater pump.
Propeller: The turbine shaft powers the propeller, which moves the ship over the water.
Large ships, like cruise ships and aircraft carriers, usually use steam turbine propulsion systems. These ships require a lot of power to move through the water, which steam turbines can supply.
Some submarines also use steam turbines. Steam engines can run very quietly, and submarines must be able to do the same. This is significant because it enables submarines to evade detection.
Steam turbines are a strong option for marine propulsion due to their high power generation, dependability, and efficiency. However, they are also costly and complicated to construct and maintain.
Steam turbines are vital to many industrial operations and contemporary electricity generation. They transform steam's thermal energy into mechanical energy, which can power machinery or produce electricity. The idea of using steam power has existed since antiquity. Hero of Alexandria created the aeolipile, an essential steam-powered device, in the first century AD as an early attempt to use steam for mechanical purposes. However, steam turbines as we know them today didn't start to take shape until the 19th century.
The late 19th century saw the development of steam turbine technology thanks to the efforts of Gustaf de Laval and Sir Charles Parsons. When Sir Charles Parsons created a prototype in 1884 that could power an electrical generator, he was frequently given credit for making the modern steam turbine. This technology was far more efficient than previous steam engines. Modern turbines still retain the design concepts of Parsons' steam turbine, which swiftly emerged as the most popular way to produce power.
Swedish engineer Gustaf de Laval greatly aided the development of steam turbines, especially high-speed turbines. His efforts during the 1880s and 1890s resulted in the development of impulse turbines, which powered their blades using the kinetic energy of steam. These advancements made the broad use of steam turbines across numerous sectors possible.
Importance in Modern Industry
These days, steam turbines are essential to the world's energy system. They produce a sizable amount of the electricity produced worldwide in thermal power plants. In a conventional thermal power plant, steam is generated either by using nuclear energy or by burning fossil fuels like coal, natural gas, or oil. After entering the turbine, the steam transforms thermal energy into mechanical energy by expanding and propelling the turbine blades. Electricity is then produced by rotating an electrical generator using this mechanical energy.
Additionally, steam turbines are essential to many industrial operations. They power pumps and compressors in the petrochemical sector, mechanical drives in the steel sector, and energy generation and machinery powering the paper sector. The dependability and efficiency of steam turbines are also highly prized in maritime propulsion systems, especially in big warships like aircraft carriers and submarines.
Due to their adaptability and efficiency, steam turbines are essential in both conventional and contemporary energy systems. Fossil fuels, nuclear power, and renewable energy sources, including biomass, geothermal, and concentrated solar power, are all compatible with them. Because of their versatility, steam turbines will remain an essential part of the world's energy mix as it moves toward more environmentally friendly energy sources.
Fundamentals of Steam Turbines
Basic Principles
The fundamental function of a steam turbine is to transform steam's thermal energy into mechanical energy. The Rankine cycle, the basic thermodynamic cycle utilized in steam turbine operations, serves as the foundation for this procedure, which is based on the laws of thermodynamics.
To put it simply, there are four primary processes involved in the Rankine cycle:
Heat Addition: Water is heated at a steady pressure in a boiler to produce steam. There is a lot of thermal energy in this high-pressure steam.
Expansion: After being driven into the turbine, the high-energy steam expands. The turbine blades rotate as a result of the expansion of the steam, which also lowers the temperature and pressure. A shaft that is attached to a mechanical device or electrical generator receives this rotational energy.
Condensation: The steam condenses back into water after cooling in a condenser after exiting the turbine.
Pumping: To restart the cycle, the condensed water is subsequently pumped back into the boiler.
A measure of a steam turbine's efficiency is how well it transforms the steam's thermal energy into mechanical energy. Variables, including temperature, steam pressure, and turbine blade design, mainly determine this efficiency.
Key Components
A number of essential parts make up steam turbines, and each one is vital to the turbine's functioning:
Rotor: The turbine's revolving component, the rotor, consists of a shaft and associated blades. Steam transforms thermal energy into mechanical energy by spinning the rotor as it moves through the turbine.
Stator: The stator is the stationary component of the turbine that encircles the rotor. It has fixed blades that efficiently guide the steam flow onto the rotor blades.
Casing: The casing surrounds the entire turbine, supporting it structurally and keeping the steam inside. Additionally, it shields the internal parts from the elements.
Blades: The turbine's blades are essential to energy conversion. Blades come in two primary varieties: moving blades attached to the rotor and fixed blades fastened to the stator. The blades' layout and design are essential to the turbine's effective functioning.
Steam Supply System: This system consists of the pipes, valves, and other parts that supply the turbine with steam at the proper temperature and pressure. It also regulates how much steam enters the turbine.
Condenser: The turbine's exhaust steam is cooled by the condenser, which then turns it back into water for the cycle's reuse. Usually, a heat exchanger is used to extract the steam's latent heat of vaporization.
Governor: The governor is a control device that modifies the steam flow to alter the turbine's speed. It guarantees that the turbine can react to variations in load demand and run at the intended speed.
Types of Steam Turbines
The design, mechanism of steam expansion, and application of steam turbines determine their classification. Among the primary kinds are:
Impulse Turbines: These turbines use nozzles to deliver high-pressure steam onto the turbine blades. The blades move as a result of the steam jets striking them, but the steam pressure stays constant while it passes over the blades. The steam's impulse force is the only source of motion for the rotor. Impulse turbines can be used to drive generators in power plants and are frequently employed in high-speed applications.
Reaction Turbines: In contrast to impulse turbines, reaction turbines make use of both the steam's impulse and the reaction force produced when the steam accelerates and expands through the rotating blades. The rotor is propelled by the pressure decrease that occurs as the steam moves through the blades. Reaction turbines are frequently seen in industrial environments and are utilized in lower-speed applications.
Condensing Turbines: These turbines are made to release steam into a condenser, where it condenses into water, typically at a lower pressure. In power generation, where maximum efficiency is needed, condensing turbines are extensively utilized.
Non-Condensing Turbines: Also referred to as back-pressure turbines, these turbines release steam at a pressure greater than atmospheric pressure. The exhaust steam can be used for other industrial processes or heating. Non-condensing turbines are frequently employed in cogeneration systems that require both process steam and power.
Extraction Turbines: These turbines are made to draw steam for heating or industrial processes at one or more locations along the turbine. The residual steam generates power as it passes through the turbine. In applications requiring steam at varying pressures, these turbines offer versatility.
Reheat Turbines: Reheat turbines use a high-pressure stage to expand steam, followed by a lower-pressure stage where the steam is further developed. Reheating increases cycle efficiency and lowers steam moisture content, both of which can lessen blade attrition.
Industrial Turbines: These are made for specific industrial uses, like powering fans, pumps, or compressors. Depending on the demands of the particular application, industrial turbines can be either impulse or reaction types.
Marine Turbines: Designed to be highly dependable and able to function in harsh circumstances at sea, marine turbines are seen in both substantial commercial ships and military boats. Usually, reaction turbines are made to power generators or propellers for propulsion.
Thermodynamics and Fluid Mechanics
Thermodynamic Cycles
Thermodynamic cycles are the foundation of steam turbine operation, and the Rankine cycle is the most crucial to comprehending how these devices function. The Rankine cycle, a closed-loop cycle that transforms heat into work and is named after William John Macquorn Rankine, is the foundation of steam turbine operations in power plants and industrial settings.
The Cycle of Rankine: There are four primary processes in the Rankine cycle:
Isentropic Compression: Pumping water, the working fluid, from a low pressure to a high pressure, requires work input, usually supplied by a pump.
Isobaric Heat Addition: To create high-pressure steam, high-pressure water is heated at a steady pressure in a boiler.
Isentropic Expansion: The turbine's rotor rotates as the high-pressure steam expands inside it. The steam's temperature and pressure decrease as it grows.
Isobaric Heat Rejection: The cycle is finished when the expanding steam condenses back into water at a steady pressure.
Reheating and regenerative feedwater heating are two techniques that can increase the Rankine cycle's efficiency.
Reheat Cycle: This process involves expanding steam in a high-pressure turbine, reheating it in a boiler, and then expanding it once more in a low-pressure turbine. This procedure lowers the moisture content at the turbine's exhaust, which in turn lessens turbine blade attrition and boosts the cycle's thermal efficiency by enabling the steam to expand throughout a wider pressure range.
Regenerative Cycle: The regenerative cycle increases efficiency by using steam collected from different stages of the turbine to preheat the feedwater entering the boiler. This reduces the amount of fuel required to heat the water to the appropriate temperature.
Combined Cycle: This cutting-edge method blends a steam turbine cycle with a gas turbine cycle. A heat recovery steam generator (HRSG) uses the gas turbine's exhaust gases to create steam, which powers a steam turbine. Very high total efficiency is possible with this configuration, frequently above 60%.
Fluid Dynamics in Steam Turbines
Since the effective conversion of steam energy into mechanical work depends on the controlled flow of steam through the turbine, fluid dynamics is essential to the operation of steam turbines.
Steam Flow and Velocity Triangles: Velocity triangles, which are geometric representations of the steam velocity in relation to the turbine blades, define the flow of steam through a turbine. Since steam passes through both stationary (stator) and moving (rotor) blades, these triangles aid in the analysis of the energy conversion process.
Absolute Velocity: The steam's velocity in relation to the turbine's stationary parts.
Relative Velocity: The steam's velocity in relation to the rotor's rotating blades.
Blade Velocity: The speed of motion of the turbine blades.
How well these velocities are adjusted to maximize energy transfer from the steam to the rotor determines the turbine's efficiency.
Principles of Impulse and Reaction: Steam turbines can function using one of these two concepts or a mix of the two.
Impulse Turbines: Before steam reaches the rotor blades, nozzles expand it, transforming its pressure energy into kinetic energy. The rotor spins because the blades absorb this kinetic energy.
Response Turbines: The steam in a response turbine experiences a pressure decrease as it travels through rotor blades that are designed to function as nozzles. A reactive force created by the pressure decrease rotates the rotor. Jet engines operate on a similar concept.
The impulse or response design is chosen depending on the particular application; many turbines use both concepts at different phases.
Expansion and Losses: Steam loses energy as it expands through the turbine due to friction, heat loss, and mechanical losses. These losses decrease the turbine's total efficiency. Optimizing turbine performance requires an understanding of and commitment to minimizing these losses.
Frictional losses: Occur as a result of steam rubbing against internal surfaces and turbine blades.
Heat Losses: Occur when steam exchanges heat with the turbine casing or the surrounding air.
Mechanical Losses: Take into account the turbine's bearing, seal, and other mechanical component losses.
To reduce these losses, sophisticated coatings and materials are employed, along with exacting manufacturing processes.
Heat Transfer Mechanisms
Heat transfer is a crucial component of steam turbine operation. It affects performance and efficiency. It involves three main heat transport mechanisms: radiation, convection, and conduction.
Conduction: Heat is transferred by conduction through solid materials, such as the turbine's blades or casing. Conduction is what happens in steam turbines when heat moves from hot steam to colder areas via the metal parts. An essential component of turbine construction is the materials' thermal conductivity, which influences the turbine's internal temperature distribution and heat transfer rate.
Convection: The process by which heat moves from a solid surface to a fluid—in this example, steam. Heat transmission from the steam to the turbine blade material happens as steam passes over the blades. A number of variables, including steam velocity, turbulence, and the blades' surface roughness, affect how efficient this operation is.
Forced Convection: When steam is pushed through a steam turbine at high speeds, forced convection occurs. Optimizing the turbine blade and flow path designs can improve heat transfer via forced convection.
Natural Convection: Although it is less common in steam turbines, natural convection can happen in places where air or steam is stationary. Controlling natural convection is crucial for both structural integrity and turbine cooling.
Radiation: The process by which electromagnetic waves transfer heat. While conduction and convection are usually more critical in steam turbines, radiation heat transfer can become substantial at very high temperatures, such as those seen in high-temperature turbines or the superheater sections of a boiler.
Thermal Radiation: Depending on their temperature, the turbine's constituent parts release thermal radiation. If insulation and other thermal management strategies are not used appropriately, this radiation may lead to heat losses.
Effective thermal management in steam turbines requires a careful balancing act between these heat transfer processes to maintain ideal operating temperatures and avoid component overheating, which can result in decreased efficiency or even failure.
Design and Manufacturing of Steam Turbines
Design Process
A thorough understanding of thermodynamics, fluid mechanics, materials science, and mechanical engineering is necessary for the intricate process of designing a steam turbine. The main objectives of steam turbine design are maximizing efficiency, guaranteeing dependability, and satisfying the particular operational needs of the application.
Thermodynamic Efficiency :
At the start of the design process, thermodynamic calculations are performed to identify the ideal operating parameters, including temperature, flow rate, and steam pressure. Engineers use these computations to ensure that each stage draws the most energy from the steam.
Blade Design: The design of turbine blades greatly influences their efficiency and dependability. Blades must be aerodynamically tuned to maximize energy extraction and minimize losses from friction, turbulence, and separation. To represent the flow of steam through the turbine, computational fluid dynamics (CFD) simulations are frequently used to precisely compute the blades' length, shape, and angle.
Material Selection: The materials used to build turbines must tolerate high temperatures, high pressures, and mechanical stresses. Strength, durability, resistance to erosion and corrosion, and the capacity to continue operating under temperature cycling are the primary criteria that influence the choice of material. Stainless steel, nickel-based superalloys, and high-strength alloys are examples of everyday materials.
Cooling and Heat Management: Cooling is a crucial design factor in high-temperature turbines, particularly those utilized in power generation. To avoid overheating and preserve structural integrity, blades, and other parts are frequently internally cooled with air or steam. In more demanding applications, advanced cooling designs like transpiration cooling or film cooling may be employed.
Rotor Dynamics and Balancing: To guarantee dependable and seamless functioning, the rotor is an essential part that needs to be carefully constructed. To prevent resonance, which could result in mechanical failure, engineers must take into consideration rotor dynamics, including the rotor's inherent frequencies. To avoid excessive vibrations, which can deteriorate bearings and other parts, the rotor must also be carefully balanced.
Sealing and Clearance Control: Reducing steam leakage between the turbine's various stages is crucial to preserving efficiency. To minimize losses, engineers create exact seals and regulate the space between moving and stationary components. Advanced sealing methods, including brush seals and labyrinth seals, are frequently employed.
Safety and Mechanical Integrity: The design must guarantee that the turbine can run safely in all anticipated circumstances, such as emergency scenarios, shutdown, and startup. Part of designing for mechanical integrity is creating components that can tolerate high mechanical loads, thermal strains, and the effects of transient circumstances like pressure surges or steam hammers.
Flexibility and Scalability: In order to accommodate varying power outputs or industrial needs, modern steam turbines are frequently designed with flexibility in mind. Additionally, this modular architecture makes component replacement and maintenance easier.
Materials Used
The materials used to build steam turbines are selected based on their resistance to harsh operating conditions, which include high pressures, temperatures, and mechanical stresses. The materials chosen determine the turbine's performance, durability, and safety.
High-Strength Alloys: Chromium-molybdenum steel and other high-strength alloys are frequently utilized for turbine rotors, casings, and other vital parts. These alloys are well-balanced in terms of strength, toughness, and resistance to thermal fatigue.
Superalloys Based on Nickel: These superalloys are commonly utilized in high-temperature areas of the turbine, like the blades and vanes in the high-pressure phases. These superalloys are perfect for applications where temperatures can reach 1000°C since they are made especially to retain their mechanical qualities at high temperatures.
Stainless Steel: Stainless steel is used for items that need to be highly resistant to corrosion, like those that are exposed to damp steam or harsh industrial settings. Because of their ability to withstand high temperatures and their resistance to oxidation, austenitic stainless steels are preferred in particular.
Ceramic Coatings: Ceramic coatings are frequently used to improve turbine blade performance at high temperatures. By lowering the quantity of heat that is conveyed to the underlying metal, these coatings act as a thermal barrier, extending the blades' lifespan and preventing thermal deterioration.
Titanium Alloys:
Because of their excellent strength-to-weight ratio and corrosion resistance, titanium alloys are occasionally utilized in low-pressure turbine blades. Their reduced density makes them useful in applications where weight reduction is crucial compared to alloys made of steel or nickel.
Creep-Resistant Materials: One major issue with steam turbines is creep, which is the propensity of materials to distort irreversibly under continuous load at high temperatures. Advanced ferritic steels and other creep-resistant materials are employed.
Manufacturing Techniques
A number of highly specialized procedures are used in the production of steam turbines to guarantee the accurate fabrication and assembly of parts that can survive harsh operating conditions. Different techniques are employed depending on the turbine's size, complexity, and particular needs.
Casting: Many steam turbine parts, especially the rotor and casing, are made by casting methods. Melted metal is poured into a mold that is fashioned like the finished product during the casting process. When the mold is removed once the metal has solidified, a rough component that is later refined is left behind. When making complex pieces like blades, where accuracy and material integrity are essential, investment casting and sand casting are popular techniques.
Forging: Another crucial manufacturing method, forging, is used to make substantial, high-integrity parts like rotors and discs. Forging aligns the grain structure of a metal workpiece by heating it and then shaping it under high pressure, improving its mechanical qualities. Generally speaking, forged parts are more robust and resistant to fatigue and creep than cast ones, which makes them perfect for high-stress turbine sections.
Machining: The majority of turbine components are machined to provide the required tolerances, surface finishes, and dimensions following casting or forging. Grinding, drilling, turning, and milling are examples of machining operations. Computer numerical control (CNC) equipment frequently ensures high precision and repeatability, particularly for parts like blades where aerodynamic qualities are crucial.
Heat Treatment: Annealing, quenching, and tempering are examples of heat treatment procedures used to improve the mechanical characteristics of turbine parts. By changing the metal's microstructure, these procedures increase the metal's strength, durability, and ability to withstand wear and thermal fatigue. Heat treatment is essential for blades that need to retain their integrity at high working temperatures.
Surface Treatments and Coatings: Turbine components frequently receive surface treatments and coatings to guard against corrosion, erosion, and high-temperature oxidation. Protective coatings are applied using methods like thermal spraying, chemical vapor deposition (CVD), and physical vapor deposition (PVD). As was previously noted, ceramic coatings are frequently used on blades to minimize heat transfer and offer thermal insulation.
Welding and combining: When assembling steam turbines, welding is an essential step, especially when combining significant portions of the casing or attaching blades to the rotor. High-strength joints with few flaws are produced using sophisticated welding processes, including electron beam welding and laser welding. These methods are particularly crucial for preserving the turbine's structural soundness in high-pressure and high-temperature scenarios.
Assembly and Balancing: After every part is produced, it is meticulously assembled. One of the most essential parts, the rotor, needs to be carefully balanced to guarantee smooth operation at high speeds. Balancing entails modifying the mass distribution around the rotor's axis to reduce vibrations. Usually, specialized balancing devices are used to measure and correct any imbalance.
Testing and Quality Control: Quality control is crucial in the production of steam turbines. Every component is put through a rigorous inspection and testing process to ensure it satisfies the requirements. Any internal or external flaws are found using non-destructive testing (NDT) techniques like dye penetrant examination, radiography, and ultrasonic testing. Performance testing, which involves operating the constructed turbine under controlled circumstances to confirm its output, efficiency, and operational stability, is another step in the process.
Final Assembly and Installation: Once all testing has been completed, the turbine is built and ready to be shipped to its installation location. Installation calls for exact alignment and calibration to guarantee that the turbine functions properly inside its intended system—be it a power plant, industrial facility, or marine vessel. Connecting the turbine to the electrical, steam supply, and other required infrastructure is part of the installation procedure.
Operation and Maintenance
Operating Conditions
Steam turbines work in harsh environments, and variables like temperature, pressure, steam quality, and load fluctuations can significantly impact their performance and longevity. Comprehending these conditions is imperative to maximizing turbine functioning and guaranteeing dependable performance.
Temperature and Pressure: High temperatures and pressures are ideal operating conditions for steam turbines. Steam enters the turbine in standard power generation applications at temperatures between 500°C and 600°C and pressures as high as 30 MPa (megapascals). Due to these severe conditions, the turbine is able to extract the most energy from the steam, but the components are subjected to significant mechanical and thermal strains.
Steam Quality: The quality of the steam entering the turbine is essential for it to operate effectively. To avoid condensation inside the turbine, which can cause blade attrition and decreased performance, the steam should ideally be dry and superheated. Saturated steam, however, may be employed in particular applications, such as nuclear power plants, necessitating careful design and management to control the risks involved.
Load Variations: Depending on the demands of the industrial process they are powering or the need for electricity, steam turbines frequently run under a variety of loads. Stable operation depends on the ability to react to load variations quickly and effectively. Turbines need to be able to ramp up or down without experiencing undue wear or damage.
Procedures for Startup and Shutdown: A steam turbine's startup and shutdown are crucial times that need to be carefully managed. To prevent thermal shocks, which can result in cracking or deformation, the turbine's components must be progressively raised to operational temperature during startup. In a similar vein, the turbine is gradually cooled during shutdown processes to avoid damage.
Control Systems: Sophisticated control systems used in contemporary steam turbines regulate several operational factors, including temperature, pressure, rotational speed, and steam flow. These mechanisms guarantee that the turbine stays within its design parameters and reacts suitably to variations in load or other operational circumstances.
Maintenance Practices
For steam turbines to remain reliable and efficient over the long term, regular maintenance is necessary. Preventive, predictive, and corrective maintain
ance are the three basic categories into which maintenance procedures are usually separated.
Preventive Maintenance: To stop possible problems from developing, the turbine must undergo routine inspections and servicing. This covers duties like:
Lubrication: To lessen wear and friction, lubricate bearings and other moving parts on a regular basis.
Inspection of Blade and Seals: Examining turbine blades and seals for indications of corrosion, erosion, or wear.
Cleaning: To keep turbine parts operating at their best, deposits or scales must be removed.
Calibration: Making sure that sensors and control systems are precisely calibrated to avoid operational errors.
Predictive maintenance: This method forecasts when maintenance is required before a failure happens by using condition monitoring techniques. Instead of using a set timetable, this method enables maintenance to be planned according to the turbine's actual condition. Important methods consist of:
Vibration Analysis: Tracking the turbine's vibrations to identify misalignments, imbalances, or bearing problems.
Thermography: The process of identifying hotspots or irregular temperature distributions that can point to an issue using infrared cameras.
Oil Analysis: Examining the lubricating oil for indications of chemical deterioration, wear particles, or pollution.
Corrective Maintenance: This type of maintenance is carried out to replace or repair damaged parts when a component breaks or an issue is discovered. Maintenance of this kind may include:
Blade Replacement: To restore turbine efficiency and stop additional damage, worn-out or damaged blades should be replaced.
Seal replacement or repair: Taking care of seal problems that could result in reduced efficiency or steam leaking.
Bearing Replacement: To avoid rotor unbalance and excessive vibrations, replace worn or damaged bearings.
Outage Planning: Steam turbines usually experience planned outages when performing thorough inspections, repairs, and overhauls. These outages are meticulously scheduled to reduce downtime and guarantee that the turbine is put back into service in the best possible condition. The turbine may be disassembled during an outage, and key parts such as the rotor, blades, and casing may be examined and repaired as needed.
Common Issues and Solutions
Even with their sturdy construction, steam turbines might have a number of problems when they're operating. Maintaining dependable performance requires quickly recognizing and resolving these problems.
Erosion and Blade Fouling: Fouling happens when deposits build up on the turbine blades, frequently as a result of steam impurities. However, high-velocity steam or water droplets that impinge on the blades create erosion, which progressively wears down the material. If ignored, these problems can result in decreased productivity and significant harm.
Solution: While erosion-resistant coatings might prolong blade life, routine cleaning, and maintenance can stop fouling. Additionally, the likelihood of these issues can be decreased by enhancing the quality of the steam that enters the turbine.
Vibration and Rotor Imbalance: Rotor imbalance, misalignment, bearing wear, and other mechanical issues can all contribute to excessive vibration, a typical problem in steam turbines. Accelerated component wear and, in extreme situations, catastrophic failure can result from vibration.
Solution: Vibration analysis and routine rotor balancing can help identify and address these problems before they result in severe damage. Regular bearing inspections and proper alignment during installation are also essential.
Steam Leakage: Cracks in the casing, worn seals, or inadequate sealing surfaces can all cause steam leakage. In addition to decreasing efficiency, this may harm nearby components.
Solution: Steam leaking can be reduced by routinely inspecting seals and replacing them as needed. Sometimes, a better seal and longer service life can be obtained by switching to more sophisticated sealing technologies, including brush seals.
Thermal Fatigue and Creep: Cracks develop as a result of thermal fatigue, which is brought on by repeatedly heating and cooling turbine parts. The slow deformation of materials under continuous high temperatures and stress is known as creep. Both problems have the potential to compromise the turbine's structural soundness seriously.
Solution: These dangers can be reduced by carefully controlling operation temperatures and using materials made especially to withstand thermal fatigue and creep. It's also crucial to conduct routine inspections and look for creep or tiredness.
Solution: Control system failures can be avoided by using redundant systems in conjunction with routine testing and calibration. Reliability can also be increased by replacing outdated systems with more contemporary digital control systems.
Applications of Steam Turbines
Power Generation
From massive thermal power plants to smaller, dispersed energy systems, steam turbines are essential to the production of electricity. The primary uses of steam turbines in power generation are described in the ensuing subsections:
Power plants powered by coal:
Summary: Historically, one of the most popular uses for steam turbines has been in coal-fired power plants. Coal is burned in a boiler to create high-pressure steam in these plants, which is subsequently fed into a steam turbine to produce power.
Function of Steam Turbines: In coal-fired power plants, steam turbines are made to withstand the high pressures and temperatures involved in burning coal. An electrical generator is powered by the mechanical energy they create from the steam's thermal energy.
Environmental Considerations: Despite their efficiency, coal-fired power plants contribute significantly to greenhouse gas emissions. To increase efficiency and lower emissions, many contemporary plants use emission control systems and are switching to cleaner coal technologies, like supercritical and ultra-supercritical steam cycles.
Nuclear Power Facilities:
Overview: The thermal energy produced by nuclear fission is transformed into electrical power in nuclear power plants using steam turbines. These facilities generate steam and heat water using atomic reactors.
Function of Steam Turbines: In contrast to fossil fuel facilities, the steam generated in nuclear reactors is usually produced at a lower temperature and pressure. However, because nuclear power generation is safety-critical, the turbines need to be incredibly dependable and long-lasting. Large turbines with high power outputs are frequently used in nuclear power plants in order to keep up with the reactor's constant energy production.
Special issues: Safety issues, such as the capacity to function dependably in the event of an emergency and resist the corrosive impacts of specific types of steam, are taken into account while designing steam turbines for nuclear power.
Combined cycle gas-fired power plants:
Overview: Gas and steam turbines are both used in combined cycle power plants to produce energy. In these plants, a steam turbine is powered by the exhaust heat from a gas turbine that produces electricity.
Function of Steam Turbines: By using the waste heat from the gas turbine, the steam turbine in a combined cycle plant increases the plant's total efficiency. This technique dramatically increases the plant's thermal efficiency, frequently rising beyond 60%.
Benefits: Compared to conventional coal-fired plants, combined cycle plants are renowned for their excellent efficiency, flexibility, and reduced carbon emissions. Steam turbines are essential to attaining these advantages in these plants.
Geothermal Energy Facilities:
Overview: Geothermal energy, or the heat stored in the Earth, is used to create electricity in geothermal power plants using steam turbines.
Function of Steam Turbines: Steam is drawn from subterranean reservoirs and utilized to power turbines in geothermal plants. These turbines need to be built to withstand the possibility of corrosive gasses and minerals, as well as steam, with different temperatures and pressures.
Problems and Solutions: Scaling, corrosion, and non-condensable gas management are the primary problems in geothermal power generation. For long-term operation in these conditions, turbine designs must incorporate corrosion-resistant materials and cutting-edge sealing technology.
Solar Thermal Power Facilities:
Overview: Steam turbines are used in solar thermal power plants, sometimes referred to as concentrating solar power (CSP) facilities, to produce electricity using solar radiation.
Function of Steam Turbines: In CSP plants, sunlight is focused by mirrors or lenses to heat a fluid, which is subsequently converted into steam. To generate electricity, steam powers a turbine, which transforms thermal energy into mechanical energy.
Innovations: Some CSP facilities incorporate thermal storage devices, which enable them to produce power even in the absence of sunlight. These plants' steam turbines need to be able to work well with the thermal storage systems and adjust to different steam inputs.
Industrial Applications
Steam turbines provide mechanical power for various applications in industrial operations and power generation.
Petrochemical Sector:
Overview: Steam turbines are crucial to the petrochemical sector. They power compressors, pumps, and other equipment required in the manufacturing of chemicals and petroleum products.
Function of Steam Turbines: under this sector, steam turbines are frequently made to run continuously, efficiently, and dependably under challenging circumstances, such as hot temps and corrosive surroundings.
Benefits: Steam turbines in petrochemical facilities contribute to increased overall energy efficiency by recovering waste heat and turning it into usable mechanical or electrical energy.
Paper & Pulp Industry:
Overview: Steam turbines are used in the pulp and paper industry to generate electricity and power mechanical processes like pulping, drying, and papermaking.
Function of Steam Turbines: In this sector, steam turbines are frequently used in cogeneration systems, which generate steam for manufacturing and electricity simultaneously. This combined heat and power (CHP) method improves energy efficiency.
Problems: The primary issues are managing varying loads and guaranteeing dependable performance in settings with high moisture content and potentially corrosive substances.
The Production of Steel:
Overview: Steam turbines power blowers, compressors, and rolling mills in the steel industry. The technique is more energy-efficient because the steam used frequently originates from waste heat recovery systems.
Function of Steam Turbines: Steam turbines help lower steel mills' total energy usage by using waste heat to produce electricity for various operations.
Benefits: Integrating steam turbines into steel production processes helps meet environmental laws while also saving energy expenses. Reducing pollutants also reduces energy expenses.
Sugar Sector:
Overview: Steam turbines are widely used in the sugar business to produce ethanol and sugar. They are a component of cogeneration systems that run on bagasse, the fibrous waste that remains after sugar juice is extracted.
Steam turbines in this sector produce electricity and supply mechanical power for crushing and refining operations. Utilizing biomass, such as bagasse, lessens reliance on fossil fuels and makes the process more sustainable.
Sustainability: The use of steam turbines in sugar manufacturing demonstrates how renewable energy sources can be used in industrial settings.
Marine Propulsion
Historically, steam turbines have been used for maritime propulsion, especially in big commercial ships and military boats. They are perfect for this demanding application because of their power production, dependability, and efficiency.
Navy Ships:
Overview: Steam turbines have historically been a key component of naval propulsion, particularly in large ships like submarines, destroyers, and aircraft carriers.
Function of Steam Turbines: Naval turbines are built to be dependable, efficient, and capable of producing large amounts of power. They are required to operate under extreme operating circumstances, including abrupt speed changes and extended high-speed operation.
Developments: Modern naval steam turbines frequently use cutting-edge materials and cooling technology to survive the severe sea environment and run silently—two qualities essential for military operations involving stealth.
Commercial Transport:
Overview: Large ships like tankers and bulk carriers in commercial shipping employ steam turbines. Steam turbines are still utilized in some applications, especially those requiring high power and long-range operation, even though diesel engines are now more prevalent.
Benefits: Compared to alternative propulsion systems, steam turbines provide smooth operation, less vibration, and less maintenance, which makes them appropriate for large ships.
Trends: As more fuel-efficient diesel engines have become available, steam turbines have been less common in commercial ships. Nonetheless, they continue to be utilized in some situations where their advantages surpass those of substitute technology.
Renewable Energy Integration
Additionally, steam turbines are being used in renewable energy systems, which helps to produce sustainable and clean energy.
Biomass Power Plants:
Overview: Biomass power plants create energy by using organic materials like garbage, wood, and agricultural residues to produce steam, which powers turbines.
Function of Steam Turbines: Steam turbines in biomass plants are required to manage steam produced from a range of biomass sources, which can differ in terms of consistency and quality. The turbines' flexible and practical design maximizes the energy that may be obtained from biomass.
Environmental Benefits: Because the CO2 absorbed during biomass growth balances the CO2 released during combustion, biomass power generation is regarded as carbon-neutral. Thanks in large part to steam turbines, this is a practical and sustainable energy source.
Concentrated Solar Power (CSP):
Overview: Solar energy is converted into electrical power in CSP plants using steam turbines. The plants focus sunlight onto a receiver using mirrors or lenses, which then heats a fluid to create steam.
Function of Steam Turbines: CSP plants' turbines need to be built to run effectively on steam produced by varying solar input and to interface with thermal storage devices, which enable power output even in the absence of sunlight.
Innovation and Future Prospects: As CSP technology develops, steam turbines are anticipated to become increasingly significant in supplying dispatchable, renewable electricity, which will help stabilize grids that heavily rely on intermittent renewable sources like solar PV and wind.
Efficiency and Performance Optimization
Factors Affecting Efficiency
An essential component of a steam turbine's operation is its efficiency, which affects the energy conversion process as a whole as well as the financial sustainability of power plants and industrial uses. A steam turbine's efficiency can be affected by a number of factors:
Steam Conditions:
Temperature and Pressure: The potential for energy extraction increases with the temperature and pressure of the steam at the turbine inlet. Because superheated steam has a higher energy content, the turbine can do more work, which boosts efficiency. Nonetheless, the design and materials used must be able to resist these harsh circumstances.
Steam Quality: Turbine performance is influenced by the quality of the steam, especially its dryness fraction. Because wet steam contains water droplets, it can erode turbine blades and decrease efficiency. These losses can be reduced by superheating the steam or by maintaining a high dryness fraction.
Aerodynamics and Design:
Blade Design: The effectiveness of turbine blades is greatly influenced by their shape, angle, and surface finish. More efficient energy conversion from steam to mechanical work is made possible by aerodynamically designed blades, which minimize losses from turbulence and friction.
Efficiency of the Stages: Steam turbines are frequently separated into several stages, each intended to draw energy from steam at increasingly lower pressures. The effectiveness of each stage influences total turbine efficiency. Optimizing efficiency requires proper staging with precisely measured blade profiles and angles.
Mechanical Damage:
Friction and Wear: Mechanical losses caused by friction in bearings, seals, and other moving parts can decrease a turbine's total efficiency. Cutting-edge materials, adequate lubrication, and routine maintenance can reduce these losses.
Vibration and Imbalance: Excessive vibrations or rotor imbalances can result in mechanical inefficiencies, as energy is wasted as undesired movements occur. It is essential to ensure that the turbine is balanced correctly and that efficient dampening systems manage vibrations.
Thermodynamic Deterioration:
Heat Losses: Heat loss occurs when steam or other elements transfer heat to the surroundings. Reducing the temperature differential inside the turbine and adequately insulating the pipes and turbine case can help lower these losses.
Entropy Generation: Optimizing the expansion process and avoiding irreversible losses within the turbine is necessary to reduce entropy, which can be increased by inefficiencies in the expansion process within the turbine stages and lower the available work output.
Optimization Techniques
Steam turbine efficiency can be increased by combining technology advancements, operational tactics, and design improvement. To improve turbine performance, the following methods are frequently employed:
Advanced Design of Blades:
Computational Fluid Dynamics (CFD): CFD is frequently utilized in turbine blade design and optimization. By modeling the steam flow through the turbine, engineers can pinpoint regions of loss and modify blade designs and angles to increase efficiency. CFD eliminates the requirement for physical prototypes by enabling the testing of several design iterations in a virtual setting.
3D Blade Profiling: Advanced manufacturing techniques like 3D printing and precision machining can produce complex blade profiles suited to particular operating circumstances. Blades that have undergone 3D profiling can achieve better aerodynamic performance and lower losses.
Control of Steam Temperature and Pressure:
Superheating and Reheating: Efficiency can be significantly increased by either reheating steam in between turbine stages or by raising the temperature of steam prior to it entering the turbine (superheating). For example, reheating lowers the moisture content in the turbine's later stages, enabling more energy extraction.
Pressure Optimization: Efficiency can be increased by running the turbine at the ideal steam pressure for each stage. The steam pressure throughout the turbine must be meticulously controlled to ensure that every stage runs at its most efficient location on the pressure-enthalpy curve.
Energy Recovery Systems:
Regenerative Feedwater Heating: This method uses steam obtained from the turbine's intermediate stages to warm the feedwater before it enters the boiler. This increases the Rankine cycle's total efficiency because less fuel is required to reach the appropriate steam temperature.
Condensate Recovery: By recovering and reusing condensate (water) from turbine exhaust, less energy is needed to heat and pressurize water for later cycles. Additionally, this reduces the need for additional water treatment, which raises total efficiency.
Optimization of Load:
Variable Load Operation: Contemporary steam turbines are built to function well under a variety of loads, not just when they are operating at maximum capacity. Power plants can increase overall efficiency by optimizing turbine performance under partial loads, particularly in applications where demand varies throughout the day.
Load matching: The process of modifying the turbine's operation to correspond with the particular energy demand at any given moment. To meet the needs of the load in real-time, this may entail regulating the turbine's output, changing the number of active turbine stages, or altering the steam flow rate.
Systems for Monitoring and Control:
Real-Time Performance Monitoring: Thanks to sophisticated sensors and control systems, temperature, pressure, vibration, and efficiency parameters may all be tracked in real-time. By regularly monitoring these parameters, operators can optimize performance and avert problems before they result in breakdowns or inefficiencies.
Predictive maintenance: Using data analytics and machine learning, predictive maintenance systems can predict possible problems based on past performance data. This allows for preventative maintenance, which lowers downtime and raises turbine efficiency overall.
Monitoring and Performance Analysis
Continuous performance data analysis and monitoring are necessary to maintain steam turbines' maximum efficiency. The methods listed below are frequently employed to evaluate and improve turbine efficiency:
Necessary Performance Measures (KPIs):
Heat Rate: The heat rate indicates how much energy the turbine uses to produce electricity. It is usually stated as the quantity of fuel energy needed per electrical output unit (e.g., BTU/kWh). Monitoring the heat rate can help identify fuel and turbine performance inefficiencies.
Thermal Efficiency: The ratio of usable work production to total heat input is known as thermal efficiency. It is a crucial sign of how well thermal energy is transformed into mechanical energy by the turbine. Higher thermal efficiency indicates better performance.
Capacity Factor: This is the ratio of the turbine's actual output over time to its maximum output potential. It shows the efficiency of the turbine's use in relation to its maximum capacity.
Tests of Performance:
Acceptance Testing: To ensure a turbine meets the required performance standards, acceptance testing is carried out either upon initial installation or following a significant overhaul. Under controlled circumstances, these tests usually examine variables, including output power, efficiency, and steam consumption.
Routine Testing: Performance tests are carried out regularly to monitor the turbine's continuous efficiency. Regular testing allows us to identify slow performance drops and take prompt action to boost productivity.
Analytics and Optimization of Data:
Data Logging and Trend Analysis: Constant data logging allows for the gathering of enormous volumes of performance data, which can then be examined to spot patterns, find irregularities, and determine how operational adjustments affect productivity.
Digital Twins: A steam turbine's virtual model that replicates its real-world equivalent in real-time is called a digital twin. By contrasting the performance of the digital twin with actual operational data, operators can find inefficiencies and test possible enhancements without endangering the actual turbine.
Tools for diagnosis:
Vibration Monitoring: A vital diagnostic technique for identifying mechanical problems such as rotor imbalance, misalignment, or bearing wear is vibration analysis. Operators can prolong the turbine's life and avoid efficiency losses by spotting and fixing these problems early.
Thermal Imaging: Thermal imaging evaluates the temperature distribution among the turbine's components and identifies hotspots. This makes it easier to spot places where heat loss is occurring and where cooling or insulation may be required.
Environmental Impact and Sustainability
Environmental Concerns
Despite being essential to industrial operations and electricity generation, steam turbines raise a number of environmental issues. The energy sources utilized to generate steam and the byproducts of turbine operation are the leading causes of these problems.
Emissions of greenhouse gases:
Fossil Fuel Combustion: Carbon dioxide (CO2) and other greenhouse gases are released mainly by steam turbines found in coal, oil, and natural gas-fired power plants. One of the leading causes of climate change and global warming is CO2, which is released when fossil fuels are burned.
Mitigation Strategies: Some ways to lower greenhouse gas emissions are increasing the efficiency of steam turbines, switching to cleaner fuels, and incorporating carbon capture and storage (CCS) technology. Because less fuel is needed to generate the same quantity of power, higher efficiency lowers emissions per unit of energy produced.
Air Pollutants:
Sulfur Dioxide (SO2) and Nitrogen Oxides (NOx): When fossil fuels are used in power plants, toxic air pollutants like SO2 and NOx are released. These pollutants can cause acid rain and respiratory issues in people. Because coal-fired power stations have a higher sulfur concentration in their fuel, these pollutants are more common there.
Control Technologies: To lower SO2 and NOx emissions from power plants, technologies like selective catalytic reduction (SCR) and flue gas desulfurization (FGD) are employed. Low-NOx burners and other methods of combustion optimization further reduce the production of these pollutants at the source.
Thermal pollution and water use:
Requirements for Cooling Water: Steam turbines, especially in large power plants, need a lot of water to cool. Removing water from natural sources may impact local ecosystems, mainly if it is not handled sustainably. Additionally, thermal pollution, which harms aquatic life, can result from the release of heated water back into the environment.
Mitigation Strategies: Power plants can use closed-loop cooling systems that minimize thermal discharge and water withdrawal to lessen these effects. Additionally, especially in areas with limited water supplies, dry cooling systems—which use air rather than water—are being used more and more.
Byproducts and Solid Waste:
Coal Ash and Slag: Solid byproducts like ash and slag, which can include heavy metals and other hazardous materials, are produced when coal is burned in power plants. Careful management of these leftovers is necessary to avoid contaminating the soil and water.
Reuse and Disposal: According to modern waste management techniques, ash can be safely disposed of in lined landfills and used to make concrete and cement, two helpful building materials. Turning waste into valuable goods can reduce coal ash's adverse environmental effects.
Sustainability Initiatives
Due to environmental concerns, the steam turbine sector is increasingly embracing sustainability measures to lessen its environmental impact and aid in the shift to a low-carbon economy.
Integrating Renewable Energy:
Biomass and Waste-to-Energy: Steam turbines are being combined with waste-to-energy facilities and biomass, two renewable energy sources. These systems generate steam from biological waste materials, which steam turbines subsequently use to generate power. Because the CO2 absorbed during biomass growth balances the CO2 released during combustion, biomass is regarded as carbon-neutral.
Geothermal and Solar Thermal: Steam turbines are another method used by geothermal and concentrated solar power (CSP) facilities to produce electricity. These renewable energy sources are appealing choices for environmentally friendly power generation since they emit few or no greenhouse gases. In these environments, the usage of steam turbines promotes the broader uptake of renewable energy technology.
Efficiency Gains:
Supercritical and Ultra-Supercritical Steam Cycles: Supercritical and ultra-supercritical steam cycles, which function at higher temperatures and pressures than traditional steam cycles, are the result of developments in turbine technology. Because these cycles are more efficient, less fuel is required to generate the same quantity of energy, which lowers emissions.
Cogeneration and Combined Heat and Power (CHP): Cogeneration, also known as CHP, systems employ the same energy source to generate both proper heat and power. CHP systems significantly increase total energy efficiency by absorbing and using steam turbine waste heat, which lowers emissions and fuel consumption.
Capturing and Storing Carbon (CCS):
CCS Technology: Carbon capture and storage, or CCS, is a system that uses CO2 emissions from factories and power plants to absorb them and keep them out of the atmosphere. The CO2 that has been caught is subsequently moved underground in geological formations. By combining CCS with steam turbines, fossil fuel-based power generation can significantly lower its carbon footprint.
Opportunities and Challenges: Although CCS can slow global warming, it has drawbacks, including high prices, energy demands, and the requirement for appropriate storage locations. Ongoing research and development initiatives, however, aim to overcome these obstacles and make CCS a practical choice for significant emission reductions.
Efficiency of Materials and Resources:
Recycling and Waste Reduction: The steam turbine sector is implementing strategies to reduce waste and boost resource effectiveness. This includes reducing material waste through precision manufacturing techniques and reusing metals and other materials used in turbine production.
Life Cycle Assessment (LCA): This method is used to analyze how a product affects the environment at every stage of its life cycle, from the extraction of raw materials to disposal. Manufacturers can find areas where environmental impacts can be minimized through life cycle assessments (LCAs), which will result in more sustainable turbine production and operation.
Regulatory Framework
Steam turbines, especially those used in power generation, must adhere to several environmental laws to reduce their environmental impact. Although these laws differ by area, they usually center on waste management, water use, and emissions reduction.
Regulations for Emissions:
U.S. Clean Air Act: The Clean Air Act (CAA) governs air pollutants from industrial sources, including steam turbines and power plants in the United States. The CAA requires the adoption of the best available control technologies (BACT) to decrease emissions and sets limitations for pollutants like SO2, NOx, and particulate matter.
EU Emissions Trading System (EU ETS): This cap-and-trade system places a cap on the overall quantity of greenhouse gases that specific industries, such as electricity generating, are permitted to emit. In the EU, steam turbine operators are required to adhere to emission allowances or buy extra allowances if they surpass them.
Regulations on Water Use and Discharge:
U.S. Clean Water Act: The Clean Water Act (CWA) establishes water quality standards and controls the release of pollutants into American waters. To prevent their operations from endangering aquatic ecosystems, power plants that use steam turbines are required to get permits for the withdrawal and release of water.
EU Water Framework Directive: The Water Framework Directive regulates water use and thermal discharges from power plants and provides a framework for safeguarding water resources throughout the EU.
Management and Disposal of Waste:
RCRA, or the Resource Conservation and Recovery Act, regulates the handling of hazardous and non-hazardous waste in the United States, including coal ash from power plants. The act promotes the recycling and reuse of industrial waste and mandates safe disposal procedures.
EU Waste Framework Directive: The EU Waste Framework Directive encourages recycling and the decrease of waste generation by establishing rules for waste management among its member states. Operators of steam turbines are required to abide by these rules in order to reduce their environmental impact.
Global Guidelines and Standards:
Environmental Management Systems: The ISO 14001 standard gives businesses a framework for methodically handling their environmental obligations. By adhering to ISO 14001, operators of steam turbines can increase sustainability and lessen their environmental impact.
World Bank Environmental and Social Standards (ESS): The World Bank's Environmental and Social Standards (ESS) provide Guidelines for controlling environmental and social risks in World Bank-financed projects. These requirements are frequently applied when building power plants and other large-scale steam turbine projects.
Future Trends and Innovations
Technological Advances
The need for increased efficiency, dependability, and environmental performance is driving the ongoing evolution of the steam turbine sector. A number of technological developments are influencing how steam turbines will develop in the future:
Advanced Substances:
Superalloys: The creation of sophisticated nickel-based superalloys is increasing the efficiency of steam turbines by allowing them to run at higher pressures and temperatures. These materials are perfect for usage in the most demanding parts of the turbine since they are made to withstand creep, corrosion, and thermal fatigue.
Ceramic Matrix Composites (CMCs): CMCs are attracting interest due to their potential to take the place of conventional metal alloys in high. Because of these materials' superior oxidation resistance, low density, and thermal stability, turbines can run at even greater temperatures without losing structural integrity.
Additive Manufacturing: Often referred to as 3D printing, additive manufacturing is transforming the way turbine parts are made. This technology allows for the creation of complex, optimized geometries that are hard or impossible to accomplish using conventional manufacturing techniques. Additionally, additive manufacturing speeds up production and minimizes material waste.
Advanced Design of Blades:
3D-Aerodynamic Blades: Steam turbine performance and efficiency are being enhanced by advancements in blade design, especially the application of 3D aerodynamic modeling. By maximizing steam flow, these blades minimize losses from friction and turbulence. Engineers can optimize blade designs with the use of computational fluid dynamics (CFD) simulations.
Shrouded and Shroudeless Blades: To increase efficiency even more, shrouded blades—which have a cover on the tips to prevent leaks—are being refined. Meanwhile, developments in shroudless blade designs are being investigated in an effort to preserve aerodynamic performance while lowering weight and mechanical complexity.
Smart Turbines with Digitalization:
Digital Twins: A virtual replica of a steam turbine that operates in tandem with the real machine is known as a "digital twin," and it is quickly emerging as a crucial instrument in the industry. With digital twins, operators can forecast maintenance requirements, improve operations, and track turbine performance in real-time. By modeling various situations, digital twins can assist in anticipating possible problems and recommending the best course of action for maintenance or operational changes.
Machine learning and artificial intelligence (AI): These two fields are increasingly being utilized to improve turbine control systems. By allowing for more accurate control over operating parameters like temperature, pressure, and steam flow, these technologies maximize turbine efficiency across a range of load scenarios. Additionally, AI-driven data can forecast equipment breakdowns, minimizing downtime and prolonging the lifespan of turbine parts.
Scalable and Modular Designs:
Modularity: The development of modular steam turbines is a movement aimed at increasing flexibility and cutting costs. Modular turbines are appropriate for both large-scale power plants and, more minor, decentralized energy systems since they are simple to scale up or down according to power generation needs. Additionally, modularity reduces downtime by making maintenance and component replacement more straightforward.
Scalability for Microgrids: Distributed energy systems and microgrids are using steam turbines. These scalable turbines are intended to supply dependable electricity in isolated areas or as a component of a hybrid energy system that combines conventional power generation with renewable energy sources.
Integration with Smart Grids
Steam turbines are being incorporated into smart grid systems, which, as the energy landscape changes, provide more flexibility, dependability, and efficiency in power generation and delivery.
Steam Turbines' Function in Smart Grids:
Load Balancing: Steam turbines are crucial to smart grid load balancing, especially during high demand. They can be turned up or down to meet demand, keeping the system stable and preventing blackouts. Because they can react swiftly to demand fluctuations, steam turbines are an important part of smart grids.
Integration with Renewable Energy: Renewable energy sources like wind and solar are being progressively integrated into smart grids. When renewable energy sources are sporadic, steam turbines—especially those found in combined heat and power (CHP) plants—can deliver backup power, guaranteeing a steady and dependable energy supply. Steam turbines can operate more efficiently by integrating with smart grid technologies, which use real-time grid data.
Advanced Control Mechanisms:
Real-Time Monitoring and Control: To make steam turbines run more effectively in a smart grid, sophisticated control systems are being created. In order to maximize performance, these systems modify operating parameters like steam pressure and temperature based on real-time data. Additionally, real-time monitoring lowers maintenance expenses and downtime by identifying possible problems before they become failures.
Grid Synchronization: To enable smooth integration with smart grids, steam turbines are being outfitted with cutting-edge synchronization technologies. By ensuring that the turbines can synchronize their output with the grid's frequency and voltage, these technologies preserve the power's dependability and quality.
Energy storage and demand response:
Demand Response Programs: These programs involve steam turbines, in which electricity generation is modified in response to current demand. With the help of these programs, steam turbines can balance the grid and lessen the need for additional peaking power plants by lowering their output during low demand or increasing it during peak times.
Integration with Energy Storage: To increase their adaptability and efficiency, steam turbines are being combined with energy storage devices like thermal storage and batteries. Energy storage increases grid stability and efficiency by enabling turbines to store excess energy generated during times of low demand and release it when needed.
Research and Development
The goal of ongoing research and development (R&D) is to advance steam turbine technology, fulfill changing energy market demands, and tackle environmental issues.
Exceptionally Effective Steam Cycles:
Supercritical and Ultra-Supercritical Cycles: Developed at greater temperatures and pressures than traditional cycles, supercritical and ultra-supercritical steam cycles are being propelled by research and development. By providing greater thermal efficiencies, these sophisticated cycles lower emissions and fuel consumption. To survive the harsh circumstances of these cycles, researchers are investigating novel materials and designs.
Thermodynamic Cycle Innovations: Novel thermodynamic cycles, such as the Organic Rankine Cycle (ORC) and the Kalina cycle, are being investigated for their capacity to increase efficiency in particular applications. These cycles employ various working fluids or configurations to maximize energy conversion, especially in low-temperature or waste heat recovery applications.
Carbon-Neutral and Low-Carbon Technologies:
Hydrogen-Fueled Steam Turbines: Research is ongoing to develop steam turbines that run on hydrogen, a carbon-free fuel that may be generated with renewable energy. Hydrogen-fueled turbines could achieve reliable, low-carbon power generation, especially when combined with renewable energy sources.
Carbon Capture Integration: One of the main areas of research focused on lowering CO2 emissions from fossil fuel-based power generation is the integration of carbon capture and storage (CCS) technology with steam turbines. The goal of ongoing research and development is to increase CCS's effectiveness and affordability so that it may be implemented on a big scale.
Improved Sturdiness and Dependability:
Advanced Coatings and Surface Treatments: Research and development is concentrated on creating advanced coatings and surface treatments that can shield turbine parts from erosion, corrosion, and high-temperature oxidation, thereby extending their lifespan. These coatings are crucial for enhancing the robustness and dependability of turbines that operate in challenging environments.
AI and Predictive Maintenance: Research into AI—and machine learning-driven predictive maintenance solutions are contributing to increased steam turbine reliability. These technologies make it possible to estimate maintenance requirements more precisely, minimizing unplanned downtime and prolonging the life of turbine components by examining past performance data and spotting trends that precede failures.
Challenges and Opportunities
The future of the steam turbine industry will be shaped by the possibilities and problems it faces as it develops.
Challenges:
Environmental rules: The steam turbine sector faces challenges from increasingly strict environmental rules, especially those pertaining to water use and greenhouse gas emissions. Continuous innovation in turbine design, materials, and operating procedures is necessary to meet these standards.
Competition from Alternative Technologies: The steam turbine sector faces competition from emerging alternative power production technologies like wind, solar, and energy storage. Policies aiming at lowering carbon emissions frequently favor these technologies, which are becoming more cost-competitive.
Aging Infrastructure: Many steam turbines, especially those in older power facilities, are nearing the end of their operating lives. Upgrading or replacing ancient turbines with more contemporary, efficient designs is quite difficult, especially in terms of downtime and expense.
Prospects:
Decarbonization Initiatives: The steam turbine sector has a chance to create low-carbon and carbon-neutral technology as a result of the worldwide movement toward decarbonization. This includes incorporating steam turbines with CCS, hydrogen, and renewable energy sources.
Energy Transition: Steam turbines have the potential to be crucial components of hybrid systems that integrate conventional power generation with renewable energy as the energy sector shifts to more sustainable sources. These hybrid systems can lower overall carbon emissions while delivering dependable, uninterrupted power.
Emerging Markets: The steam turbine sector has a lot of room to grow in emerging markets, especially in Asia and Africa. The need for dependable and effective power generation technologies, such as steam turbines, is anticipated to rise as these areas continue to industrialize and develop their energy infrastructure.
Case Studies and Industry Examples
Notable Projects
Steam turbines' practical uses demonstrate their adaptability and effectiveness in a range of sectors. The case studies that follow demonstrate noteworthy installations and the effects of steam turbines in various contexts:
Taiwan's Taichung Power Plant:
Overview: Located in Taiwan, the Taichung Power Plant is one of the biggest coal-fired power plants globally. With a 5,500 MW installed capacity, it is essential to supply Taiwan's industry and population with energy.
Function of Steam Turbines: The plant employs several sizable steam turbines to generate electricity from the thermal energy of burning coal. Supercritical steam conditions optimize energy extraction by operating these turbines at high efficiency.
Environmental Impact: Taichung has reduced its environmental impact by implementing cutting-edge pollution control technology, such as selective catalytic reduction and flue gas desulfurization, even though it is a coal-fired plant. The facility also acts as a standard for increasing the efficiency of large-scale fossil fuel power generation.
Kenya's Olkaria Geothermal Plant:
Overview: Situated in Kenya's Great Rift Valley, the Olkaria Geothermal facility is Africa's largest geothermal power plant. It has a capacity of more than 800 MW and makes a substantial contribution to Kenya's renewable energy mix.
Function of Steam Turbines: The plant uses steam turbines created especially to deal with the particular difficulties presented by geothermal steam, including the presence of corrosive gases and minerals. By effectively converting geothermal energy into electrical power, the turbines offer a dependable power source with little carbon emissions.
Sustainability: In areas with geothermal resources, the Olkaria Geothermal Plant's success shows how geothermal energy may be used to provide baseload power sustainably. The facility's growth throughout time demonstrates the scalability of geothermal projects and the vital role steam turbines play in this field of renewable energy.
The United States Ivanpah Solar Electric Generating System:
Overview: Situated in the Mojave Desert of California, Ivanpah is one of the most considerable concentrated solar power (CSP) installations in the world. With a 392 MW capacity, it generates steam to power turbines by focusing sunlight onto boilers using mirrors.
Function of Steam Turbines: Ivanpah's steam turbines are built to run on the variable steam input feature of CSP reactors. Because of their rapid start and stop capabilities in reaction to solar conditions, they are essential in the conversion of solar energy into electrical power.
Innovation: Ivanpah illustrates the successful integration of steam turbines into renewable energy sources. Using cutting-edge steam turbine technology, the project shows how CSP technology can deliver utility-scale renewable electricity.
Industry Leaders
Numerous businesses and organizations have contributed to the development and application of steam turbines. These pioneers in the field have established standards for dependability and efficiency and led the way in technological developments.
Siemens Power:
Overview: Siemens Energy is a world leader in the design and production of steam turbines. Its portfolio comprises turbines for industrial use, marine propulsion, and power generation. The business is renowned for emphasizing efficiency and innovation.
Major Contributions: Siemens has led the way in creating high-efficiency steam turbines, including those for use in supercritical and ultra-supercritical environments. Power plants worldwide use their turbines extensively, supporting both renewable energy and fossil fuel projects. Leading the way in digitization, Siemens provides sophisticated monitoring and control solutions that improve turbine dependability and performance.
GE, or General Electric:
Overview: With a long history of engineering prowess and invention, General Electric is another significant force in the steam turbine sector. Power generation, industrial operations, and marine propulsion are just a few of the uses for GE's steam turbines.
Key Contributions: By creating high-performance blades, cutting-edge materials, and integrated control systems, GE has significantly increased turbine efficiency. In order to help operators maximize turbine performance and lower operating expenses, the business has also been a pioneer in the application of digital twins and predictive maintenance technology.
Power from Mitsubishi:
Overview: One of the top producers of steam turbines, especially in Asia, is Mitsubishi Power, a division of Mitsubishi Heavy Industries. The company provides a variety of turbines for power generation, including those for renewable energy projects and coal, nuclear, and gas-fired plants.
Important Contributions: Mitsubishi Power is renowned for its cutting-edge steam turbine designs that prioritize dependability and efficiency. The business has advanced the development of ultra-supercritical turbines and has been instrumental in implementing massive geothermal and biomass projects. Additionally, Mitsubishi Power is actively engaged in research and development projects centered on carbon capture integration and hydrogen-powered turbines.
Lessons Learned
The use of steam turbines in a variety of industries offers essential insights into the difficulties and ideal procedures related to these technologies. These undertakings have taught us important lessons, such as:
The Value of Personalization
Project-Specific Design: The necessity of customization is among the most significant takeaways from successful steam turbine projects. Every project has different needs depending on the fuel type, operational conditions, and environmental standards. For the steam turbine to operate as efficiently and reliably as possible, its design must be adjusted to these particular circumstances.
Adaptation to Local Conditions: Long-term success in projects like the Olkaria Geothermal Plant depended on the turbine design being modified to manage the unique properties of geothermal steam, such as its high moisture content and corrosive gasses. This emphasizes how crucial it is to comprehend local variables and take them into account when designing turbines.
Efficiency as a Primary Motivator:
Emphasis on Efficiency: The necessity to lower pollutants and fuel consumption has made efficiency enhancements a top priority in the development of steam turbines. Supercritical and ultra-supercritical steam conditions can significantly increase efficiency, resulting in cheaper operating costs and a minor environmental effect, as shown by projects like the Taichung Power Plant.
Innovation in Blade Design: Developments in blade design, such as 3D-aerodynamic blades and the utilization of cutting-edge materials, have made increasing turbine efficiency possible. Industry titans like Siemens and GE have taught us that turbine components must be continuously innovated to stay competitive in the market.
Digitalization's Function:Embracing Digital Technologies: In the steam turbine business, integrating digital technologies—like AI, digital twins, and real-time monitoring systems—has become a best practice. By predicting maintenance requirements, minimizing downtime, and optimizing performance, these technologies help operators increase overall dependability and efficiency.
Data-Driven Decision-Making: Employing data analytics to track turbine performance and anticipate possible problems is becoming increasingly crucial. Leaders in the field have shown that data-driven decision-making may greatly increase steam turbine lifespan and operational efficiency.
Environmental Compliance and Sustainability:
Sustainability Initiatives: As sustainability has gained more attention, steam turbine projects are using cleaner energy sources, including biomass, geothermal, and solar thermal. If combined with the right technologies, steam turbines can be a major component of the shift to renewable energy, as demonstrated by lessons learned from projects like Ivanpah.
Regulatory Compliance: One of the most important aspects of steam turbine projects is ensuring that environmental standards are followed. The Taichung Power Plant's effective deployment of emission control systems emphasizes how crucial it is to follow legal requirements to reduce environmental impact and guarantee project viability.
Conclusion
Summary of Key Points
For more than a century, steam turbines have been a mainstay of industrial and power generation applications, exhibiting exceptional versatility and efficiency in a range of contexts. This thorough examination of steam turbines has addressed their development over time, basic concepts, design and manufacturing procedures, and the diverse range of applications they find use in.
Basics: Steam turbines work by transforming steam's thermal energy into mechanical energy, which can be utilized to power machinery or produce electricity. Steam temperature, blade design, and the thermodynamic cycles used—the most popular being the Rankine cycle—all affect the efficiency of this operation.
Design and Manufacturing: Thermodynamics, materials science, and mechanical engineering must all be carefully considered during the intricate process of designing steam turbines. Turbine efficiency and dependability are increasing due to developments in blade design and digitization, as well as advancements in materials like superalloys and ceramic matrix composites. Casting, forging, machining, and heat treatment are all steps in the production process that guarantee turbines can survive harsh operating environments.
Operation and Maintenance: To guarantee their longevity and optimal performance, steam turbines need to be operated carefully and receive routine maintenance. Problems like steam leakage, rotor imbalance, and blade attrition can be avoided with the use of sophisticated diagnostic equipment and maintenance techniques, including predictive and preventive maintenance. Proper operation, which includes controlling the quality of the steam and following starting and shutdown protocols, is also necessary to optimize efficiency and reduce wear.
Applications: Steam turbines are employed in many different processes in the steel, petrochemical, and pulp and paper industries as well as in power generation in coal, nuclear, and geothermal plants. Additionally, they are essential for naval propulsion and are being used more and more in renewable energy sources like biomass and concentrated solar power.
Efficiency and Optimization: The performance of steam turbines is largely determined by their efficiency, which is continuously improved by developments in energy recovery systems, steam conditions, and blade design. Digital twins, artificial intelligence, and real-time monitoring systems are improving the ability to maximize turbine performance, minimize downtime, and prolong the lifespan of turbine components.
Sustainability and Environmental Impact: Steam turbines' effects on the environment, especially those driven by fossil fuels, are a major worry. However, these effects are being lessened, and the shift to a low-carbon future is being supported by sustainability measures like the use of carbon capture technology, the development of supercritical and ultra-supercritical steam cycles, and the integration of renewable energy sources.
Future Trends and Innovations: The steam turbine sector is expected to experience further innovation in the years to come, driven by developments in digitalization, materials science, and smart grid integration. Research into low-carbon and carbon-neutral technology, such as increased carbon capture systems and turbines powered by hydrogen, will significantly aid the industry's development. The industry faces both potential and challenges due to aging infrastructure, competition from alternative technologies, and environmental laws.
The Future of Steam Turbines
Steam turbines will continue to be essential to industrial operations and power generation as the world's energy landscape changes. Thanks to their capacity to adjust to evolving technology, integrate with renewable energy sources, and increase efficiency, they will remain relevant in the ensuing decades.
The drive for decarbonization and the demand for more environmentally friendly energy sources will fuel further advancements in steam turbine technology. Meeting the increasing need for clean, dependable, and efficient power will require the development of ultra-efficient steam cycles, the incorporation of digital technologies, and the investigation of novel materials and designs.
Furthermore, steam turbines provide substantial growth potential in emerging economies and in hybrid energy systems that blend conventional power generation with renewable resources. The need for steam turbines that can provide high efficiency, dependability, and sustainability will grow as these areas continue to industrialize and develop their energy infrastructure.
In summary, steam turbines have a long history of invention and adaptability. As they develop further in response to the opportunities and challenges of the twenty-first century, their future is bright. Steam turbines will continue to be a vital component of the world's energy generation for many years to come thanks to the continuous efforts to increase efficiency, lessen their adverse effects on the environment, and integrate with cutting-edge energy systems.
Introduction to Power Generation with Steam Turbines
For more than a century, steam turbines have been the mainstay of power generation. Invented by Sir Charles Parsons in 1884, steam turbines swiftly rose to prominence as the primary method of transforming thermal energy into mechanical energy and then electrical energy. Due to their efficiency and adaptability, they are the foundation of electricity generation globally.
Steam turbines are employed in many different contexts in contemporary power generation, ranging from massive fossil fuel facilities to renewable energy installations. Their working idea is to drive a rotor coupled to a generator to transform the energy from high-pressure steam into mechanical energy. Because of their adaptability, steam turbines can be used in a variety of energy systems, such as solar thermal, geothermal, coal, nuclear, and natural gas power plants.
The capacity of steam turbines to effectively generate substantial amounts of electricity is what makes them significant. As technology has advanced, steam turbines can now function at higher pressures and temperatures, which boosts efficiency and lowers fuel usage. Steam turbines are an essential part of the shift to more sustainable energy systems because of these advancements, which have also resulted in a decrease in greenhouse gas emissions per unit of electricity produced.
Types of Power Plants Using Steam Turbines
Coal-Fired Power Plants
One of the most popular uses for steam turbines is in coal-fired power plants. In these plants, coal is burned in a boiler to create high-pressure steam, which is subsequently fed into a steam turbine to produce power. Despite its negative environmental effects, including CO2 emissions and air pollution, coal is still a major source of energy, especially in developing nations.
As steam turbine technology has advanced over time, coal-fired power plants have become more efficient. Higher thermal efficiency is made possible by supercritical and ultra-supercritical steam conditions, in which steam is produced at pressures and temperatures above the critical point. This lessens the total impact on the environment because more electricity can be created from the same amount of coal.
Emission control methods like selective catalytic reduction (SCR) and flue gas desulfurization (FGD) are used to lower pollutants like SO2 and NOx emissions. Furthermore, although they are still in the early phases of adoption, carbon capture and storage (CCS) technologies are being developed to absorb CO2 emissions from coal plants.
Nuclear Power Plants
Steam turbines are essential for turning nuclear fission heat into electrical power in nuclear power plants. Water is heated in nuclear reactors to create steam, which powers a steam turbine that is connected to a generator. Because nuclear energy is safety-critical, the steam turbines used in nuclear power facilities are usually enormous and require a high degree of reliability.
One of the main issues in nuclear power generation is managing the steam conditions, which are different from those in fossil fuel plants. Specific turbine designs must function well in nuclear reactors because the steam they produce is frequently at lower temperatures and pressures. The turbines also need to be able to survive radiation and function in a very regulated environment.
The design of the steam cycle impacts nuclear power plant efficiency; some use reheat cycles to increase thermal efficiency. Advances in materials and turbine design bring about ongoing improvements in steam turbine performance in atomic applications, improving the overall dependability and safety of nuclear power generation.
Gas-Fired Power Plants (Combined Cycle)
Combined-cycle power plants represent a significant development in the application of steam turbines. To increase efficiency, these plants combine a steam turbine and a gas turbine. A gas turbine produces electricity in a combined-cycle system, and the waste heat from the gas turbine's exhaust is converted to steam, which powers a steam turbine to produce even more electricity.
Among all power production technologies, combined cycle power plants have one of the most excellent efficiency rates, frequently surpassing 60%. This is so because the energy that would otherwise be wasted as waste heat is efficiently captured and used by the steam turbine. Because they can swiftly ramp up or down in response to variations in the demand for electricity, combined cycle plants are also more adaptable than conventional power plants.
Natural gas has become a more appealing alternative for power generation due to the use of steam turbines in combined cycle facilities, especially in nations seeking to lessen their dependency on coal and cut carbon emissions. Combined cycle plants are an essential part of the contemporary energy mix since they may combine gas and steam turbines in a single plant, increasing efficiency and reducing environmental impact.
Geothermal Power Plants
Steam turbines are essential to producing electricity in geothermal power plants, which use the Earth's natural heat. Turbines in these facilities are powered by steam drawn from subterranean reservoirs. Because corrosive gases and minerals are frequently present in geothermal steam, turbine design and operation face particular difficulties.
The temperature and pressure of the geothermal steam determine the efficiency of geothermal power plants. Resources with higher temperatures can employ more effective steam cycles, such as those found in fossil fuel plants. Turbines that can manage a more excellent range of steam quality are necessary for geothermal plants, which generally operate at lower pressures.
Because geothermal resources are available around the clock, one of the main benefits of geothermal energy is its capacity to supply baseload power. Geothermal facilities' steam turbines need to be sturdy and dependable in order to run constantly with little downtime. Geothermal energy is becoming a more significant component of the renewable energy landscape as a result of advancements in turbine materials and designs that increase the durability and efficiency of geothermal turbines.
Concentrated Solar Power (CSP) Plants
Utilizing mirrors or lenses, Concentrated Solar Power (CSP) plants direct sunlight onto a receiver, which uses it to heat a fluid and create steam. Subsequently, this steam powers a turbine to produce energy. Because thermal storage devices store heat for later use, CSP is unusual among renewable energy sources in that it can generate electricity even when the sun isn't shining.
Because the amount of sunshine can change throughout the day, the steam turbines used in CSP facilities are made to run on fluctuating steam inputs. To match the amount of solar energy available, the turbines must be able to start and stop swiftly and effectively. Steam turbines with sophisticated blade designs and materials that can tolerate the thermal cycling brought on by sporadic solar input are frequently used in CSP systems.
One of the significant advancements in CSP is the incorporation of molten salt thermal storage, which enables the plant to store heat during the day and use it to produce steam at night or during overcast conditions. Particularly in areas with high solar irradiation, CSP with steam turbines is a valuable addition to the renewable energy mix because of its capacity to deliver dispatchable power.
Efficiency Considerations in Steam Turbine Power Generation
Since efficiency affects how well fuel or energy resources are transformed into electricity, it is a crucial component in steam turbine power generation. Steam turbine efficiency is influenced by several factors, such as operational tactics, technology developments, and thermodynamic principles.
Thermodynamic Efficiency
Thermodynamic principles, especially the Rankine cycle, the fundamental cycle utilized in steam power plants, have a significant influence on a steam turbine's efficiency. Isentropic compression, isobaric heat addition, isentropic expansion, and isobaric heat rejection are the four primary processes that make up the Rankine cycle. There are various ways to increase this cycle's efficiency:
Reheating and superheating: Rising the steam's temperature (superheating) before it enters the turbine or warming it up in between turbine stages can greatly increase efficiency by lowering the steam's moisture content and increasing the amount of energy that can be recovered.
Increased Pressure Ratios: By running the turbine at more significant pressures, more energy can be recovered from the steam, increasing cycle efficiency overall. The highest efficiency levels in contemporary power plants are found in supercritical and ultra-supercritical steam settings, where steam is produced at pressures higher than the critical point.
Regenerative Feedwater Heating: By using the steam from the turbine's intermediate stages to warm the feedwater before it enters the boiler, less fuel is used to generate steam, increasing the power plant's overall efficiency.
Technological Advances
Developments in steam turbine technology have significantly increased efficiency. Thanks to advancements in blade design, materials, and manufacturing processes, turbines can now function at higher temperatures and pressures, increasing the efficiency of energy conversion.
Advanced Blade Designs: Turbine blade efficiency is greatly influenced by their design. Modern blades are aerodynamically tuned to minimize losses from friction and turbulence. By utilizing computational fluid dynamics (CFD), engineers can create blades that optimize steam energy extraction.
High-Performance Materials: Steam turbines can now run at greater temperatures without losing structural integrity because of the development of cutting-edge materials like ceramic matrix composites and nickel-based superalloys. By preventing creep, corrosion, and thermal fatigue, these materials enable longer-lasting and more effective turbine operation.
Precision manufacturing and 3D printing: Additive manufacturing technologies, including 3D printing, have made it possible to produce turbine parts with intricate geometries that are efficiency-optimized. Turbine component uniformity and dependability are increased, and material waste is decreased, thanks to precision manufacturing procedures.
Operational Strategies
Optimizing the efficiency of steam turbines also heavily relies on operational tactics. Power plant operators can optimize steam turbine performance by carefully controlling operating parameters and load profiles.
Optimization of Load: Steam turbines function best when they are running at or close to their design capacity. However, electricity plants frequently encounter fluctuating demand throughout the day. By managing the turbine's load, operators can sustain high efficiency even during times of reduced demand. Strategies like load matching and peak shaving are used to ensure turbines run within their ideal range.
Real-Time Monitoring and Control: Thanks to sophisticated monitoring and control systems, operators of contemporary steam turbines can modify operational parameters in real-time. These systems track performance parameters, including steam temperature, pressure, and flow rate, using sensors and data analytics. By consistently tweaking these parameters, operators can increase productivity and stop problems before they cause performance losses.
Maintenance and Dependability: Regular maintenance is necessary to keep steam turbines operating efficiently. Predictive maintenance helps reduce downtime and guarantees that turbines continue to run at their best efficiency by using data analytics to identify when components are likely to fail. An efficient maintenance plan must include vibration analysis, blade inspection, and proper lubrication.
Environmental Impact and Mitigation Strategies
Although steam turbines are essential for producing electricity, they also pose a threat to the environment, mainly when they are run on fossil fuels. Understanding and reducing these effects is crucial for steam turbines to operate sustainably.
Greenhouse Gas Emissions
One major source of CO2 emissions is the burning of fossil fuels in steam turbines, especially in coal—and gas-fired power plants. Reducing the carbon footprint of steam turbine power generation is essential because these greenhouse gas emissions contribute to climate change and global warming.
Carbon capture and storage, or CCS, absorbs CO2 emissions from power stations and stores them underground in geological formations. When combined with steam turbines, CCS can drastically lower the carbon emissions of fossil fuel-based power generation. Even though CCS adoption is still in its infancy, research and development efforts are being made to increase its scalability and cost-effectiveness.
Switch to Low-Carbon Fuels: Another way to cut greenhouse gas emissions is to switch from coal to lower-carbon fuels, like natural gas, or even carbon-neutral fuels, like biomass. Compared to conventional coal-fired power plants, combined-cycle power plants, which use both gas and steam engines, offer greater efficiency and reduced emissions.
Air and Water Pollution
Fossil fuel combustion in steam turbines produces other air pollutants, such as sulfur dioxide (SO2), nitrogen oxides (NOx), and particulate matter, in addition to CO2. These pollutants contribute to acid rain, smog, and respiratory problems in humans.
Emission Control Technologies: To lower SO2 and NOx emissions from power plants, technologies like selective catalytic reduction (SCR) and flue gas desulfurization (FGD) are employed. Baghouse filters and electrostatic precipitators are two methods for controlling particulate pollution. These innovations lessen the negative effects of steam turbine air pollution on the environment.
Water Use and Thermal Pollution: Because steam turbines need a lot of water to cool, they may affect nearby water supplies. Aquatic ecosystems may also be impacted by thermal pollution, which is the release of heated water back into the environment. Power plants are increasingly using closed-loop cooling systems, which decrease water withdrawal and reduce thermal discharge, to address these problems. Particularly in areas with limited water supplies, dry cooling systems—which use air rather than water—are also being used.
Renewable Energy Integration
Integrating steam turbines with renewable energy sources can lessen the environmental impact of electricity generation. It is feasible to generate electricity with a reduced carbon footprint by utilizing steam turbines in combination with renewable energy technologies, including biomass, geothermal, and concentrated solar power (CSP).
Biomass Power Generation: Biomass power plants generate steam that powers turbines by using organic materials, including garbage, wood, and agricultural residues. Because the CO2 absorbed during biomass growth balances the CO2 released during combustion, biomass is regarded as carbon-neutral. A sustainable substitute for fossil fuels, steam turbines are essential in turning biomass energy into electrical power.
Geothermal and Solar Thermal: CSP facilities employ concentrated sunlight to create steam, whereas geothermal power plants use the Earth's natural heat. In both technologies, steam turbines transform thermal energy into electrical power. These renewable energy sources are appealing choices for environmentally friendly power generation since they emit few or no greenhouse gases.
Future Trends and Innovations in Steam Turbine Power Generation
The steam turbine sector is constantly changing as emerging trends and technology influence the direction of power production. In an evolving energy market, these advances aim to increase steam turbines' flexibility, efficiency, and environmental impact.
Decarbonization Initiatives
As the globe decarbonizes, steam turbines are being modified to run on low-carbon and carbon-neutral fuels. Hydrogen, in particular, is promising as a steam turbine fuel.
Hydrogen-Fueled Steam Turbines: Hydrogen is a carbon-free fuel that may be created by electrolysis utilizing renewable energy. Developments are being made to develop steam turbines that run on hydrogen, either by itself or in conjunction with other fuels. When used in combination with renewable energy sources, hydrogen-fueled turbines have the potential to generate dependable, low-carbon electricity.
Hybrid Energy Systems: Hybrid energy systems combine conventional power generation with renewable energy sources, and they are increasingly including steam turbines. These devices can lower carbon emissions while supplying power continuously. A hybrid system might combine solar or wind energy with a natural gas-fired steam turbine, which would provide backup power in the event that renewable energy sources are sporadic.
Digitalization and Smart Grids
Steam turbines are operating more effectively, dependably, and responsively to grid demands thanks to digital technologies.
Artificial Intelligence and Machine Learning: AI and machine learning are being utilized to enhance turbine operations by evaluating data from sensors and control systems. By modifying operating parameters in real time, these technologies can enhance efficiency, optimize load distribution, and forecast maintenance requirements. Additionally, AI-driven analytics are assisting in the discovery of patterns and trends that may improve turbine performance and decision-making.
Digital Twins: The idea of a digital twin—a computerized representation of a steam turbine that operates concurrently with the real machine—is gaining traction in the sector. With the help of digital twins, operators may simulate various scenarios, optimize operations, and keep an eye on turbine performance in real time without endangering the actual turbine. This technology is beneficial for anticipating and averting problems before they arise, which lowers maintenance expenses and downtime.
Integration with the Smart Grid: Steam turbines are being incorporated into innovative grid systems, which provide increased power distribution and generation flexibility and efficiency. Thanks to sophisticated control systems and real-time monitoring, steam turbines can react swiftly to variations in energy demand, helping to maintain grid balance and avoid blackouts. Combining steam turbines with energy storage devices, such as batteries, improves grid stability and makes it possible to use renewable energy sources more effectively.
Research and Development
The goal of ongoing research and development (R&D) is to advance steam turbine technology, fulfill changing energy market demands, and tackle environmental issues.
High-Efficiency Steam Cycles: Supercritical and ultra-supercritical steam cycles, which run at greater temperatures and pressures than traditional cycles, are being developed primarily through research and development—higher thermal efficiencies provided by these sophisticated cycles lower emissions and fuel consumption. In order to increase their viability for broad adoption, researchers are investigating novel materials and designs that can endure the harsh conditions of these cycles.
Carbon Capture Integration: One of the main areas of research focused on lowering CO2 emissions from fossil fuel-based power generation is the integration of carbon capture and storage (CCS) technology with steam turbines. The goal of ongoing research and development is to increase CCS's effectiveness and affordability so that it may be implemented on a big scale.
Advanced Materials and Coatings: To increase the robustness and efficiency of steam turbines, new materials, and coatings that can resist high temperatures and corrosive environments must be developed. The development of sophisticated coatings, including anti-corrosion and thermal barrier coatings, is extending the lifespan of turbine parts and lowering maintenance expenses.
Conclusion
For more than a century, steam turbines have been a vital component of power generation, and their function constantly alters in response to shifting energy demands and environmental issues. This thorough review of steam turbine power generation emphasizes the adaptability, effectiveness, and sustainability of steam turbines in a variety of applications.
Steam turbines are essential for generating dependable and effective electricity from nuclear and coal-fired power plants and renewable energy sources such as concentrated solar and geothermal. Supercritical steam cycles, sophisticated blade designs, and digitalization are only a few examples of technological developments that have greatly enhanced the efficiency and environmental friendliness of steam turbines.
Steam turbines will be crucial to decarbonization efforts as the world moves toward a low-carbon economy. Steam turbines are being modified to satisfy the needs of a more sustainable energy future in several ways, including the incorporation of hydrogen as a fuel, the use of carbon capture technology, and the creation of hybrid energy systems.
With continuous research and development propelling further advancements in efficiency, dependability, and environmental performance, steam turbines have a promising future. Steam turbines will become even more connected with innovative grid systems as digital technologies like artificial intelligence (AI) and digital twins proliferate, increasing their adaptability and responsiveness to shifting energy demands.
To sum up, steam turbines will continue to be an essential part of the world's power generation for many years to come. They will continue to be crucial in the shift to a more robust and sustainable energy system because of their capacity to integrate with renewable energy sources and adjust to new technology.