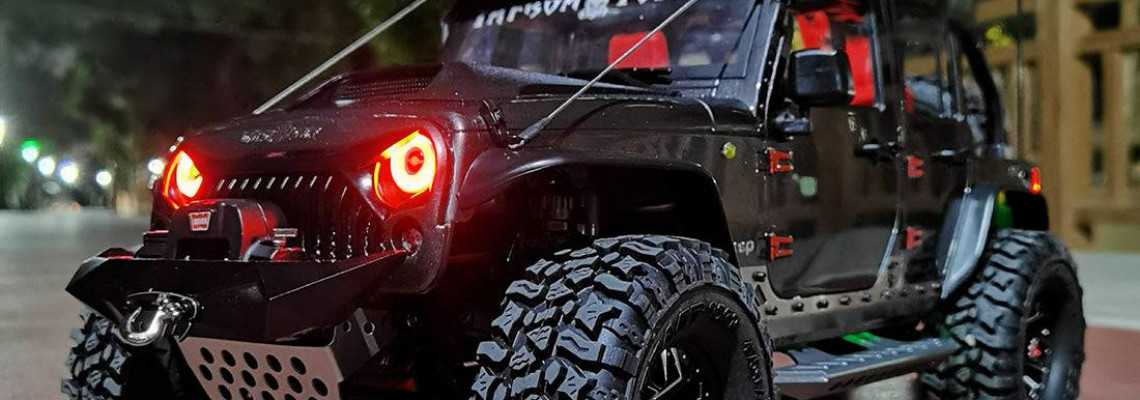
ESC Survival Guide: Preventing Failures for Ultimate R/C Performance
As is well known, electronic speed controllers, or ESCs, are crucial parts of the remote-controlled car industry. An ESC's primary job is to receive signals from a control source, like a microcontroller or radio transmitter, and then modify the power sent to the motor to control its direction and speed. ESCs are crucial to these systems because they enable accurate motor control and seamless operation.
ESCs can differ in their precise design and construction and are usually made up of multiple electronic components:
Printed Circuit Board (PCB): The PCB is an ESC's primary structural element. It offers the required electrical connections and is a platform for attaching different electronic components. To conduct electrical impulses, the PCB is frequently constructed from fiberglass with copper lines.
Microcontroller: The microcontroller or microprocessor in ESCs manages the control algorithms, decodes input device signals (such as a receiver in remote-controlled applications), and controls the motor's power supply. This microcontroller may be a key part of the ESC.
Electronic switches known as MOSFETs (Metal-Oxide-Semiconductor Field-Effect Transistors) regulate the current that flows from the battery to the motor. They are essential in controlling the motor's direction and speed. The ESC's power handling capacity can affect the quantity and calibre of MOSFETs.
Capacitors and Other Passive Components: A variety of capacitors, resistors, and inductors are employed to filter and stabilize electrical impulses. This lowers electrical noise and guarantees smooth motor running.
Connectors: ESCs are equipped with motor output and battery power input connectors. The size and type of these connectors might change according to application and voltage needs.
Heat Sink: Many high-power ESCs, particularly those found in high-performance RC cars, may have a heat sink to disperse heat produced during operation. This guarantees the ESC operates effectively and helps avoid overheating.
Protective Casing: Certain ESCs are housed in a protective metal or plastic casing to protect the electronics from physical harm and environmental influences.
Solder joints and wires: The PCB's components are connected by various solder joints and wires. These connections must be sturdy and well-designed to manage the electrical currents and voltages involved.
Battery Polarity Reversal:
Connecting the battery lines backwards is one of the most frequent causes of ESC failure. This error may result in a short circuit that harms the internal parts of the ESC. Before connecting your battery, always make sure the polarity is correct.
Labelling your batteries is a simple method of preventing battery polarity reversal: Label your batteries properly with a permanent pen. Put "+" and "-" symbols on the actual batteries. This will make determining the polarity simple.
Excessive Current Draw:
When the electrical parts of an RC (radio-controlled) car use more current (amperage) than intended, this is referred to as excessive current draw. This may have several detrimental effects, such as:
Overheating: Electrical components, including the motor, battery, and ESC (Electronic Speed Controller), may overheat due to excessive current demand. Overheating can shorten these components' lifespan or cause irreversible damage.
Decreased Efficiency: If the RC car draws more current than is required, its overall efficiency may suffer. This indicates that battery power is not being utilized as effectively as it may be, which leads to decreased performance, more stress on electrical parts, and shorter run lengths.
Stress on the Battery: Excessive current demand can shorten the battery's lifespan by causing a short circuit (and fire!). It can also produce excessive heat. Additionally, it may result in a voltage drop that impairs the vehicle's performance.
Reduced Run Time: RC fans may find it aggravating when excessive current consumption reduces run times on a single battery charge.
Component Damage: The car's motor, ESC, and other electronics may sustain damage or even fail due to prolonged and repetitive excessive current draw.
Extreme situations involving an excessive current draw may present safety problems, including the possibility of fire or other electrical hazards.
DEEP DIVE: What exactly causes excessive current draw??? Various factors cause it, let's review them:
- Mechanical Resistance: When the motor must exert more effort to overcome excessive friction in the drivetrain, such as soiled or damaged bearings or a misaligned transmission, the current draw may increase.
- Binding or Sticking Components: If any parts, such as axles, gears, or suspension sections, are binding or sticking, the motor may use more current than usual.
- Tires, shock absorbers, and bushings are low-quality or worn-out components that raise rolling resistance and increase current consumption.
- Incorrect Gear Ratio: If the gear ratio is not suitable for the kind of driving you're doing (such as off-road versus on-road), the motor may work too hard and draw too much electricity.
- Overloading the Vehicle: When an RC car gains weight, such as larger batteries, the engine must work harder to drive the extra mass, which raises the current draw. Or utilizing an ESC, battery, or motor that is too small.
- Battery problems: If the battery is worn out, broken, or has a lower capacity, the motor may need to draw more current to reach the required speed or performance.
- A mismatch between the motor and ESC (Electronic Speed Controller): If the motor and ESC are not properly matched, the ESC may not be able to manage the motor's power demands, which can lead to excessive current draw.
- Electronic Problems: A malfunctioning electronic component, such as a servo, receiver, or ESC, might cause unpredictable behaviour in an RC car and a higher current draw on the ESC's BEC.
- Tyre Selection: When the car fails to maintain grip, using tyres that are not appropriate for the terrain might lead to poor traction and excessive current draw. The current draw will rise as the tyre's weight or diameter increases.
- Driving Style: If the motor and battery are not built to withstand such demands, aggressive driving, fast acceleration, and continuous full-throttle operation may increase current draw.
To ensure you keep under the suggested current limitations for the motor, ESC, battery, and other parts, it's crucial to refer to the manufacturer's specifications and instructions. Furthermore, since overheating is frequently a noticeable sign of this problem, keeping an eye on the temperature of these parts while they are operating—keep the ESC and motor temperatures UNDER 200°F, preferably 180°F or lower; LiPo batteries should not exceed 130°F—can serve as a valuable indicator of whether excessive current is being drawn.
These infrared thermometers are explicitly made for use with R/C engines, motors, battery packs, battery chargers, electronic speed controllers, and hundreds of other applications, so having one on hand is always helpful. Aim the thermometer at the target and hit the measurement button to quickly and conveniently show the surface temperatures.
High Battery Voltage:
A catastrophic failure may occur if a battery has a voltage higher than the ESC's maximum rating (for example, a 6s pack with a 4s capable ESC). To prevent overloading the ESC, always make sure the battery voltage and the ESC's voltage rating match. (A motor overheating or possibly catastrophic motor and/or ESC failure can occur when the voltage rating is exceeded.)
Insufficient Cooling:
ESCs are no exception to the rule that heat is an enemy of electronics. Inadequate cooling may cause the ESC to overheat and malfunction. For high-power configurations, ensure adequate ventilation and consider including extra cooling components like fans or heat sinks. High-quality batteries, an ideal gear ratio, additional ventilation, and routine maintenance (removing dirt and debris) can also ensure a cooler operating vehicle.
Excessive Ripple Voltage/Current:
Instability and ESC failure may result from high ripple voltage or current in the battery-supplied power to the ESC. To reduce ripple, use high-quality batteries with low internal resistance and make sure your power connections are safe and interference-free.
Many Castle controllers can measure and record battery voltage at the start and finish of the FET cycles. The Castle Graph Viewer application on a Windows computer (or smartphone) can display this voltage swing in volts. During routine operation, the ripple voltage should be 5% or less and 10% or less during extreme manoeuvres. Any amount above this is excessive. This can be calculated by dividing the ESC's measured ripple by your battery pack's nominal voltage.
Long Battery Leads:
Overly lengthy battery leads can lower the ESC's efficiency by increasing resistance and causing voltage drops. Make every wire as short as you can, especially the ones that connect the motor and the ESC. The total length of wire between the battery and ESC (including the wire currently on the ESC and battery) should not exceed 18 inches.
Improper Wire Gauge and Connectors:
Overheating and voltage dips can result from connectors that are unable to manage the current or from wires that are too thin. Always use premium connectors and the wire gauge advised for your configuration.
Inadequate battery connectors can hamper performance. Avoid the typical "white plastic" connectors found on many battery packs. Often, a high-performance brushless system will draw the power these connectors can safely handle. Purchase connector sets designed for robust electric systems, including our QS8 antispark connectors, Castle Polarized Connectors, or CC Bullets.
Higher voltage electric power systems require silicone-coated copper wire with a high strand count. Because V8engineforsale's wire has a lower resistance than solid copper of the same diameter, more power may be transferred from the batteries to the motor with less squandered heat. Because of its highly high strand count and silicone coating, the wire is extremely flexible, preventing breakage and work hardening over time.
In summary, use the best connectors and batteries available. The quality of the batteries will increase your Castle system's punch, runtime, and power to the ground.
Improper Soldering:
ESC failure may result from sporadic connections or shorts brought on by poor soldering. Use the proper soldering techniques and check for problems in your solder joints.
When soldering connectors, ensure the following:
1. Make use of a good soldering station. Typically, soldering stations feature a variable temperature control that allows you to adjust the heat used. A solder junction that receives too little heat will be cold, whereas a component that receives too much heat may sustain significant damage. Temperature and time are crucial components of good soldering. We are in the 350° to 400° C (660° to 750° F) range for the majority of R/C applications; 100+ Watts is advised.
2. Use premium rosin core solder. Flux, which is added to rosin core solder, helps clean the surfaces you are soldering and improves adhesion.
3. The total length of wire between the battery and ESC (including the wire currently on the ESC and battery) should not be greater than any more inches.
4. Avoid soldering wires straight onto the circuit board. This will void the warranty and harm the ESC.
5. You can click this link to wire and get the right wire gauge for your Castle ESC by clicking the application chart at http://www.v8engineforsale.com.
Exceeding BEC Limits:
Many ESCs have a built-in battery eliminator circuit (BEC) that powers the servos and receiver. However, the ESC's performance is impacted by voltage drops caused by attaching too many high-power servos or devices beyond the BEC's capabilities.
If you are slow to actuate, glitch, or brownout, it might be time to use an external BEC (battery eliminator circuit). This situation may arise when an ESC lacks an internal BEC or when the internal BEC that is there is insufficient in an application that uses powerful servos (or additional torque-increasing modifications).
The primary function of a BEC is to extract voltage from the motor batteries and reduce it to a level appropriate for your servos and receiver. An external BEC will guarantee that you are not underpowered and supply clean, steady power.
Installing a BEC is pretty simple, but if you mind a little soldering, Install instructions are included with our BECs.
Would you like to know how to quickly test your external BEC to ensure it can safely run everything you have powering?
Step 1: Unplug the motor.
Step 2: Plug in a newly charged battery pack (the same one you'll use with the CC BEC) and turn on your transmitter.
Step 3: For 20 seconds, exercise every servo simultaneously (switch on and off other devices). If you see the servos slowing to a crawl or stopping or the LED on the BEC blinking quickly, you use more current than the CC BEC can safely manage.
Conclusion:
Understanding the causes of electronic speed controller failure is crucial for a seamless and pleasurable hobby experience. Electronic speed controllers are vital parts of RC cars and drones. You may prolong the life of your ESCs and experience trouble-free operation by steering clear of typical dangers, including reverse battery connections, excessive current draw, high voltage, and poor cooling. When configuring your electronic speed controller for your RC adventures, adhere to best practices and consult the manufacturer's literature for detailed instructions and suggestions for your ESC model.